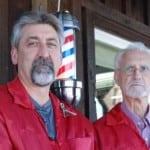
10 Sure Signs Your Company Just Doesn’t Understand Equipment Reliability!
In honor of the fast approaching holiday season, let’s start the week off with a laugh or two, I have listed some of the sure-fire signs that your company may not be ready for this reliability stuff. I have to say that in my first 5 years working as a consultant, I wasn’t prepared for some of the things folks would tell me while working on site, and there were times I actually laughed when I should have just bitten my tongue. I once asked a manager if their equipment was reliable; he pondered the question a minute and replied, “It is some of the time.”
Tell me: how do you not laugh when someone says that with a straight face?
Understanding now that while these are all real observations, the most important thing about this journey is simply the recognition that we need to improve, and in beginning this journey, we sometimes fail to recognize just how far we need to go.
That being said, here are the Top 10 Signs Your Company Just Doesn’t Get Reliability!
- You can’t or don’t plan or schedule any of your maintenance work and have come up with a number of excuses as to why planning and scheduling works at thousands of plants around the world but it won’t work at your site.
- That Predictive Maintenance stuff won’t work here because our stuff is supposed to vibrate! While some folks might laugh at this, I hear this one a few times each year. I can add to it a few others, including: “You won’t be able to hear our air leaks with that Ultraprobe. We got so many steam leaks, it just won’t work.” It has taken me a number of years to learn not to laugh when I hear these statements; now, I just smile and politely explain how each technology works even with background noise and vibration.
- You firmly believe that the human senses are far better calibrated for detecting potential failures! At a site this year, someone informed me that they did not need oil analysis: “We got old Jim here; he has been lubin’ our equipment for 20 years and he can taste when the oil is goin’ bad.” Old Jim proudly nodded his head in approval and when I asked if this was food grade oil he was sampling, he said: “Well, I suppose you could use it in food when it’s new, but when it’s goin’ bad, I’m guessing it would ruin most anything you put it in!”
- You believe the only reason things fail is because they weren’t made big enough or strong enough. A good poker face is important here as well. Sometimes it’s a mechanical linkage, a fuse, or overload, but in most cases it’s the belief that we need a larger pump, motor, gearbox, or chain. It’s at this time that we pull them back in and work to determine what is causing the component to fail.
- You believe your plant or industry vertical is different, and as a result, it’s not possible to have reliable equipment. I used to hear this one a couple of times each year, but over the last 10 years, the message has gotten out that regardless of how nasty it is at your site, there are still dozens of ways to improve reliability. “But you don’t understand, Doug; this is (add industry vertical). Our equipment is just going to fail from time to time because of the rough environment.” My reply: so it’s tougher than outer space, the temperature is colder than it is at 40,000 feet, or it’s hotter than it is when an aircraft has to re-enter Earth’s atmosphere? It’s under more pressure or vacuum than one might have to deal with 5,000 feet below the surface of the ocean? Because somehow, for each of those harsh environments, engineers have managed to design and improve on equipment that operates in that environment.
- You believe the best maintenance guy is the one who can fix it the fastest! In fact, that same guy is the highest paid maintenance guy; he or she might even be the maintenance supervisor, and he/she has come up with dozens of unique ideas to help replace broken equipment faster. Mr./Ms. Speedy are very critical of others who try to take the time to think things through to ensure the job is safe or seek to understand why the equipment may have failed.
- Your managers and Human Resources department believe the maintenance and operations folks can easily be replaced by a temp, contractor, or anyone else who may or may not have a high school diploma. The people who believe this never say it out loud; it might hurt someone’s feelings. They instead demonstrate it in the way they interact with these groups on a daily basis. You won’t find them in the break room or sitting at the same lunch table. When they do have to go into the plant to look at a piece of equipment or talk to someone, that time is kept to a minimum; and in meetings with their peers, they openly express that the problem with the company is that the right people aren’t working with the equipment.
- You make darn sure that all couplings are “flex” couplings because they don’t need precision alignment! This one speaks for itself. If you really believe a flex coupling takes away the need to perform precision alignment, you’re in the wrong business.
- The maintenance shop has one torque wrench, just in case one of the guys needs it! It pains me to admit that this is true for more than 50% of the plants I visit. If someone is able to find the torque wrench, the likelihood that it has been calibrated in the last year is slim. Ask these same folks if they believe in and practice precision maintenance techniques and most will say that they do. With the cost of a good torque wrench at somewhere between $150 and $200, I am still confused as to why all your maintenance folks aren’t required to have and use one.
- The general belief is that we don’t have the time or the money to do things like RCM and RCA. The truth of the matter is that most places got to where they are today because they didn’t spend the time and money up front using the reliability tools that identify and mitigate failure modes during the design phase of their plant. They then waited for things to fail before they saw a need to assess spare parts or develop some type of informal maintenance strategy. At that point, the best viable option was to learn how to fix it faster and try to perfect your component replacement skills. It might be the most expensive maintenance strategy there is, but it gets lots of attention; and while we don’t have a lot of money to spend, we somehow find enough to fix it when the machine is no longer running.
So there you have it! I’m sure there are a lot of you who could add to this list, so feel free to drop a comment or send an email if you get a chance
Great, great, great. I love this article. All here written is completely true. Many people beleive equipment won’t fail if well designed or are strong enough. People who don’t beleive in RCM or RCA because they don’t know a clue about it. Only listen and repeat.
Agreed; however, AR&M are important though part of the greater supportabily equation. Several years ago I took over as Chief Engineer in a UK Defence Company. The great cry was ‘Design for Manufacture’. That’s fine for an immediate urgent requirement. However, for projects predicted for in service to up to 50 years is short sighted. Integrated Logistic Support (ILS) and Logistic Support Analysis (LSA) are the prerequisite for return on long term investment. Through life support normally constituted 45% of a programme’s total cost. ILS and LSA planning are essential in any programme or project. Prediction on ranging & scaling of spares is fundamental to return on investment. Buy to few; pay dearly for reordering. Buy too many and they languish as expensive shelfware through to disposal. There are over 20 areas of ILS, including R&M. Verification & Valdation; ITEAP, Obsolesence Management, Facilities, Packaging Handling Storage & Transportation, configuration management, Training for operators & maintainers, Technical Documentation, Manpower, Human Factors are examples. Yes; R&M is key as is Reliability planning, FMECA, RCA and maintainability. Disposal and termination is also not fully predicted resulting in enduring costs on storage ‘out of use’ due to environmental legislation. Rant over; keep the mantra alive!?
Well said Roly and thanks for sharing your insights/experience. cheers, Fred
Thanks. I get a bit intennse on this issue. ?