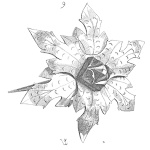
To increase reliability, you need to decrease the chances of failure occurring. Each chance of failure creates risk. Operating risk can be mitigated and managed by meeting all 15 Precision Maintenance excellence targets.
This list of precision maintenance excellence targets is how to ensure component parts, and the equipment they are in, always operate with optimal reliability. Each requirement must be met to the highest standard. By doing this your equipment and machinery are operating with the least microstructure stress possible and getting utmost reliability.
Precision Standard Requirement | Target | Tolerance | |
1 | Chemically correct, Contaminant-Free Lubricant | Right viscosity;0ppm water;12/_/_ to ISO4406 | <100ppm water<14/ |
2 | Precise Fits and Tolerance at Operating Temperature | <Form IT5;Temperature to design | <IT7 |
3 | Shafts, Bearings, Couplings Run Precise to Centre | <IT5 | <IT7 |
4 | Distortion-Free Equipment for its Entire Lifetime | <IT5 | <IT7 |
5 | Forces and Loads into Rigid Mounts and Supports | <IT5;No Softfoot | <IT7;Two shims |
6 | Precise Shaft Alignment at Operating Temperature | Coupling / Feet offset <10µm / 20µm | <20µm / 40µm |
7 | Precisely Balanced Rotating Parts | <G1 | <G2.5 |
8 | Least Total Machine Vibration | <1.5mm/s rms | <2.5mm/s |
9 | Precise Torques and Tensions in all Components | ±5% of correct tension | ±10% of correct tension |
10 | Correct Tools in Precise Condition to do quality work | As new and calibrated | As new and calibrated |
11 | Only In-specification Parts | OEM spec material and design | To OEM specifications |
12 | Precision Skills and Techniques | Competent to precision standards | Competent to precision |
13 | Failure Cause Removal | Creative Disassembly; Precision Assembly | Creative Disassembly |
14 | Proof Test for Precision Assembly Quality | Every task quality on TARGET | Milestones in TOLERANCE |
15 | Quality assurance system to make all the above happen together, forevermore | ACE 3T Quality System | ITP (Inspection & Test Plan) |
With Plant Wellness Way EAM methodology, each precision maintenance excellence standard has an associated target value. The target is set at a world class quality standard and found in books written by experts on each specific requirement.
To help guide your company towards this Target value, a Tolerance is specified. This Tolerance indicates the variation allowed for each PM excellence standard. Tolerance values are as per international engineering standards and original equipment manufacturer’s technical and operating manuals.
Achieving all 15 precision standard requirements concurrently is how you guarantee your equipment and machinery to operate and perform to their utmost reliability. The last requirement—establishing a work quality assurance system—is necessary to ensure all the other precision maintenance excellence standards are achieved and sustained for the lifetime of your operating assets.
Leave a Reply