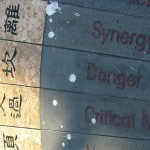
Making the criticality analysis work for you and drive improvements in the maintenance strategy
Most manufacturers do not have an up to date criticality analysis and those that do have one, do not use it to drive decisions. Having a criticality analysis facilitates improved decision making and prioritization within the site and business.
How many times are there debates regarding which work needs to be done, which PMs will be dropped from the schedule because the planned downtime was reduced? These debates occur regularly, but to not have to occur. A criticality analysis drives improvements in the business by:
- Determining the Maintenance Approach by establishing activities that must take place for each category of risk. This ensures that the business is protected from the risk by having the right risk reduction activities in place (see figure xx). In the extreme risk category, it may call for redesign of the equipment, redundant systems or online monitoring and at the low end of the categories, it may call for the equipment to be run to failure.
- Systematically reduce risk by addressing the highest risk equipment. This is taking the previous activity one step further by actively working to reduce the risk of the highest ranking equipment, regardless what the criticality is. This can be accomplished through small systematic changes in procedures, policies or through CAPEX. By having a process in place to reduce risk, the business becomes more stable and can improve profitability.
- Guide Scheduling activities by determining which work will make the biggest difference to the business. When there are numerous jobs on the schedule, and there is only time for one, how is the job chosen? Often times it is picked based on who is yelling the loudest. With an up to date criticality analysis, the work can first be sorted by the highest risk equipment. With the highest risk equipment selected, the high priority work on that equipment should be selected. This goes without saying that the equipment must be available for maintenance. This approach is often referred to as Ranking Index of Maintenance Expenditures (RIME). RIME is typically embedded in the maintenance scheduling process.
Establishing and using a criticality analysis will not eliminate the risk from the business but support in decision making and allow the business to begin to mitigate the risk in a systematic approach. Even if the business applies the criticality analysis as outlines above, it will not completely eliminate risk. Risk will always be present, but it can be reduced.
Do you use your Criticality Analysis? If so, how do you use your Criticality Analysis? If you are not using it, why not? Please share your comments as everyone benefits when we share our collective knowledge.
Remember, to find success, you must first solve the problem, then achieve the implementation of the solution, and finally sustain winning results.
I’m James Kovacevic
HP RELIABILITY
Solve, Achieve, Sustain
Leave a Reply