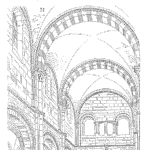
It is possible to use the circuit design or the circuit itself to evaluate electronics. This ranges from checking if the system is wired correctly (the right parts are present and attached properly) to a complex evaluation including the proper functioning of firmware and attached software.
Beyond visual inspection, we need a way to evaluate the microscopic structures with today’s electronic components.
The ability to provide inputs and measure outputs provides one view and in most cases is nondestructive.
Simulation
Simulating a circuit starts with circuit analysis (I learned the basics of this in college as an electrical engineering student) which can be accomplished by hand. Today tools are able to simulate complex circuits over many variations of inputs, component variations, and environmental conditions.
Simulation models first check on function and may include timing, effects of aging or drift, and the effects of generated electromagnetic fields (sneak circuit analysis).
For complex integrated circuits (IC) there are dedicated hardware systems to simulated the operation of an IC design.
BIST and BIT
Built in Self Test and the Built-in Test generally place the device in a test mode and run a set of commands that exercise all (most) of the circuits and operations of the device. For example, the BIT may command a lamp to illuminate and sense the voltage drop as an indication the lamp is present.
BIST and BIT require programming, space and design allowances to operate. The benefit is the ability to verify correct operation on an ongoing basis.
These tests can also be run by technicians as part of a troubleshooting or diagnostic evaluation of a system.
In Process and ICT Tests
In-Circuit Test (ICT) and In Process Testing tests energies circuits on a circuit board and measures responses at select points. Generally done with a system of probes that measure circuit values using a complex set of inputs and measurements. Often done during printed circuit board & assembly construction to verify electrical connection occurs where expected and not otherwise.
A basic test determines opens and shorts. More complex ICTs may determine individual parameter values of select components. The testing may require the addition of test points on the surface of the circuit layout to accommodate testing.
EMI/EMC Tests
Electromagnetic Interference and Electromagnetic Compatibility testing evaluate a design’s ability to operate as expected in the presence of some level of external effects. When electrical current occurs an electromagnetic field is generated by the trace or wire (a simplistic explanation) and has the potential to create current flow or voltage variation in other nearby devices. High-frequency circuits are particularly active in the creation of these fields and may require shielding to prevent transmission of potentially harmful effects.
Since it occurs, each design should be able to operate in the presence of some level of electromagnetic radiation. EMI and EMC testing provide a way to determine if the device meets (often regulatory set) requirements for the expected use environment.
The testing generally consists of exposing the device to specific strengths and type of electromagnetic radiation and measure its ability to operate.
Summary
This is a very brief summary and entire books, professional societies and business operate based on providing knowledge and equipment to perform each of the listed types of testing.
These four approaches are part of our common reliability engineering toolkit and provide information on the design, assembly, and operation of devices.
Related:
8 Nondestructive Evaluation Techniques (article)
Reliability Block Diagrams Overview and Value (article)
Root cause knowledge and models (article)
Please keep in mind the EMI/EMC Tests can be destructive.
The two most common tests where hardware is damaged are surge immunity and electrostatic discharge.
Agree. If the design is not able to withstand some threshold, we find out by the damage it causes. And, if you increase the stress eventually it will cause damage.
Cheers,
Fred