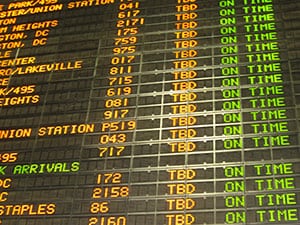
Making Maintenance Scheduling Simple
Coordinating all of the maintenance activities within a site can be overwhelming. A schedule is supposed to help reduce the sense of being overwhelmed. But why is it that when trying to pull together a schedule for the next shift, day or week, it always seems to be a mad dash?
Often times the maintenance scheduling process is not well defined or thought out, and this leads to being overwhelmed. It also projects an image to our operational partners that we do not have our house in order. This image may or may not play a role in having our Maintenance windows moved or cancelled, further our scheduling issues.
Having a simple, easy to use scheduling process can reduce the mad dash and enable us to project an image of being in control of our work. This leads to trust with the Operations planning team, creating an integrate schedule.
When I first starting working with a site, the site was very reactive; the Planner/Scheduler was trying to put together the weekly schedule at 7:00pm on a Friday night. Come Monday the schedule would change so much that it was unrecognizable. During some discussions, the Operations teams stated that when Maintenance as given windows, they weren’t used or the equipment ran worse than before.
Obviously they did not believe in the maintenance department, and had no problem changing their schedule. When I discussed this with the maintenance team, they stated they had issues resourcing the windows as Operations always moved the windows without consulting them. A vicious cycle indeed.
To put a stop to this cycle, we immediately begin defining a simple, easy to use scheduling system. This scheduling approach works by using horizons. Horizons are different levels of scheduling that build on one another, resulting in a long reaching, easy to utilize approach. It all begins with the;
52 Week Schedule: The 52 week schedule provide the foundation of the Scheduling Horizon system. It enables the operation to focus on the exceptions, not the norms. Once properly defined, the 52 week schedule support an integrating scheduling with operations. So what exactly is it?
The 52 week schedule is a high level view of the reoccurring work. This includes PMs, Overhauls, Inspections, etc. Any work that is known to be required over the course of an average year. Once the reoccurring work has been identified, it needs to be leveled. This ensures there is a consistent amount of reoccurring work each week. This level work load establishes the equipment requirements each week. It also allows the Shutdowns to be identified within an approximate timeline. This can be integrated with the operations scheduling to further define equipment requirements. An important note with 52 week scheduling. Specific work orders are not identified during this horizon. The schedule only looks at capacity requirements.
Once the reoccurring work load foundation is in place, the system can be started using the;
Daily Prioritization Meeting: The Daily Prioritization Meeting involves the Planner/Scheduler and the Maintenance Supervisor. During this meeting all new request are reviewed using a simple logic diagram, which defines when the work should be scheduled, using the horizons.
Using this approach with the horizons, the Planning group can begin to build a high level schedule for the next 16 weeks. This also enables the Planner to prioritization their own activities as well.
16 Week: As work is prioritized, it begins to fill the 16 weeks. This allows the site to develop a short term strategic plan. Utilizing this 16 week schedule, a robust schedule can be develop with operations, identifying which process or systems can be planned down for a particular week.
During the horizon, all reoccurring work and all newly identified work is specified with work orders. This enables the Planner/Scheduler to identify material, resource and equipment constraints and work to optimize the schedule. Any given week from week 5 to 16 has approx. 60% of capacity filled with work.
4 Week: The 4 week schedule is the high level tactical schedule. During this period the exact dates and times of the planned downtime windows are finalized with operations. The Planner/Scheduler continues to refine the schedule and finalize all material and resource availability issues. During week 2 to 4 approx. 80% of the capacity has been filled with work.
1 Week: The Tactical Schedule. The 1 week schedule is typically a snip of the 4 week schedule. It is during this time that 100% of capacity is filled with work, resulting from priority corrective and breakdown work, along with pulling ahead any work as needed. This is the last horizon that the Planner/Scheduler will touch the schedule. It is then handed over to the Maintenance Supervisor(s) at least 3 days before the start of the week.
Day / Shift: The Day/Shift schedule is managed by the Maintenance Supervisor(s). They have the schedule for the week, and know their crew. Giving the Maintenance Supervisor(s) the ability to manage the work on his crew allows them to address any manpower & operational issues, and providing the best service for the business.
Initially this approach is a bit time consuming as the work is leveled, and the new Daily Prioritization Meeting is adopted. But based on experience, the approach will reduce the stress and time to produce a workable schedule, resulting in more time to develop better job plans, and reduce wrench time barriers.
How do you manage your Maintenance Scheduling? Do you use horizons or just put the work in the first available slot? What is your largest challenge in Maintenance Scheduling? I highly encourage you to share your feedback.
Remember, to find success, you must first solve the problem, then achieve the implementation of the solution, and finally sustain winning results.
I’m James Kovacevic
HP RELIABILITY
Solve, Achieve, Sustain
No Fields Found.
Please provide more information on article
Hi Leslie,
What kind of additional information are you looking for here?
cheers,
Fred