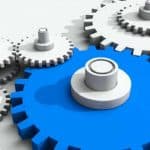
Any maintenance manager at a manufacturing plant or facility is likely aware of the problems caused by faulty equipment. Even if just one piece of equipment out of thousands breaks down, it could cause your entire operation to come to a halt. Preventive maintenance involves scheduling various maintenance activities to keep your equipment in peak condition and prevent breakdowns and failure. EAM/CMMS software is an essential tool for scheduling preventive maintenance and monitoring performance. The following are 5 tips to improve preventive maintenance with maintenance management software.
1. Establish standards
In order to develop an effective maintenance management plan, it’s important to outline detailed preventive maintenance procedures and schedules as well as establish standards for measuring performance and improving efficiency. Standard preventive maintenance lists and charts that your software vendor provides should only be used as a guideline to start. You must develop a preventive maintenance process that is unique to your organization.
2. Get all stakeholders involved
EAM/CMMS software alone will not improve preventive maintenance programs. In order to achieve an effective maintenance management process, you must refine the software to fit your process and get stakeholders involved to ensure that the software meets everyone’s needs.
3. Evaluate your current strengths and weaknesses
Prior to implementing new maintenance software, evaluate your current preventive maintenance plan’s strengths and weaknesses to determine what your organization’s most pressing needs are. Factors to consider include preventive maintenance and work procedures, equipment history, inventory, and maintenance costs.
4. Create a detailed preventive maintenance checklist
A preventive maintenance checklist consists of step-by-step instructions for maintenance technicians to follow when completing a preventive maintenance job. A comprehensive preventive maintenance checklist also shows what preventive maintenance work was performed on a given asset and allows maintenance technicians to provide feedback to the planner and supervisor. The feedback that maintenance technicians provide on a preventive maintenance checklist is valuable and can help improve future work orders.
5. Fine-tune your preventive maintenance schedule
EAM/CMMS software generates automated reminders and preventive maintenance work orders. However, it can be challenging for maintenance technicians to balance preventive maintenance work orders on a combination of assets that includes new equipment and old, poorly running equipment. Maintenance technicians are more likely to ignore new equipment since it’s running smoothly and focus on fixing older equipment instead.
It’s acceptable to skip preventive maintenance tasks for new equipment that’s showing no signs of problems, but maintenance technicians should continue monitoring the performance of the equipment regardless. You may eventually need to resume a more regular preventive maintenance schedule for that piece of equipment.
Improve Preventive Maintenance with EAM/CMMS Software
DPSI offers EAM/CMMS software for a variety of industries including facilities, fleet, manufacturing and more. Our maintenance software can help you improve preventive maintenance and achieve an optimal ROI from your assets. Contact DPSI today for preventative maintenance software free trial.
Leave a Reply