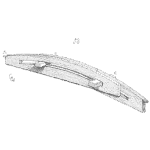
A computerised maintenance management system (CMMS) is the maintenance department’s most important tool. It provides insight into the behaviour of the facility’s individual assets, i.e. the plant and equipment. For a CMMS to be of use it must be used as an information ‘bank’ that can be investigated. There are 9 really good reasons to use a CMMS. And each one of them alone makes a CMMS worth having.
Keywords: asset management, preventative, preventive
1. A Diary and Personal Organiser Tool.
The CMMS becomes your diary. In it you record the future maintenance requirements of your assets. You use the CMMS to organise your day, your week and even the coming year. You can organise all your future jobs in detail – from the 1-hour preventative maintenance routine to the 4-week bi or tri-annual shutdown. Just be sure to review the work when it comes around to insure it is still well founded. In most businesses a year is a long time and things can change and make the old plan invalid.
Into the CMMS you enter all your resource requirements such as cranes, scaffolding, lighting towers, etc. You enter all your manpower requirements so you can organise enough people with the right skills. You enter all the parts and materials you will need for each job. You can also record the interactions that need to be taken between departments and across departments so that the jobs run ‘smooth as silk’ and no one forgets something important.
2. A Smart, Time-saving Buying Tool
A CMMS loaded up with the Bills of Materials (or the Application Parts Lists) of the equipment in the plant and the material supplier catalogues is a huge money and time saver. It’s a money saver because you can compare costs across suppliers for the same part and get the right part at the best price. It’s a time saver because you only need one or two key strokes and all the purchase description typing is done for you in correctly described ‘supplier speak’ with all the right part numbers. This makes receiving the right parts on time so much simpler and more certain.
On top of that there are dozens of phone calls to suppliers saved daily. These benefits translate to hours of effort saved each week for years to come.
3. A Cost Monitoring Tool
A CMMS will let you see where your maintenance money is going. Most maintenance budgets are also spent on plant improvements, safety improvements, environmental improvements, small capital jobs and site security. This is great to know when the budget is overspent. With this information all you need to do is point out how much extra, unbudgeted work is forced onto maintenance by the demands of the business.
The other important cost monitoring benefit of a CMMS is when jobs go bad. It’s useful to pull out the cost of labour, parts, contractors, etc for review and discussion. No one likes being reminder of a poor showing but if something good can be pulled out of the mess then everyone learns and moves forward to a better result next time.
4. Equipment Failure Analysis Tool
When at least a year’s worth of history is in a CMMS it becomes a powerful tool to spot problems. Make sure your CMMS can download its records into a spreadsheet package. Once the job or history descriptions for each asset are in the spreadsheet you can sort by keyword and spot reoccurring problems. For example I know that in one of my plants I have 44 problems that have reoccurred consistently in the last 3 years. I can describe them exactly to you and I can point out what they are.
Now that is a powerful bit of knowledge to know – isn’t it! You can bet that as soon as I can get the time and resources available we will start working on those problems one-by-one, from the most expensive to the least expensive, till they are gone. But I would never have known where to put my efforts without the CMMS.
5. A Trending Tool
A CMMS will let you look at the maintenance side of your business by permitting you to trend any data you want. You can trend by cost, hours, equipment type, specific asset, etc. A lot of CMMS are poor at providing trending tools themselves (they were not designed for that job). In that case make sure your CMMS can drop the data into a spreadsheet package in a format that can be read and interrogated and do the trending in the spreadsheet. It is absolutely amazing what you can learn and better understand when you can display numbers as a graph.
6. A Teaching, Training, Instruction-giving Tool
The CMMS lets you ‘talk’ directly to the operators and maintainers. You can tell them anything you want about the asset that they have to work on and the way in which you want the job done. You can add in pictures, drawings, cross-section details, material specifications, step-by-step job instructions, etc. You can turn the CMMS into a tool for getting the job done right first time! This will make everyone’s day better and happier.
7. A Safer Work Place
You get big safety benefits with a CMMS. You can automatically provide MSDS* for your people, you can advise them on safe work practices, they can be warned of how to handle dangers in the plant, all the necessary permits can be printed out at the one time, etc.
Personal safety is a strong selling point to operators and maintainers and it is a good idea to include safety benefits when trying to convince people to use a CMMS. One idea that works is to tie the Permit to Start Work to the work order for a job. This forces everyone to use the CMMS for their own safety.
8. Accounting Benefits
There are many accounting benefits that also accrue to CMMS users. Faster invoice matching, fewer invoices, better cash flow projecting, more accurate budgeting, tighter cost control, etc can all be achieved.
9. Production and Operations Benefits
A CMMS is not just for maintainers. The production people can use it as a tool to help them run their plant better. You can use a CMMS to pop-out reminders for operators to clean strainers, to perform monitoring duties, to clean out tanks before the sediment gets too thick, etc.
A CMMS is a smart tool for smart people.
Mike Sondalini – Maintenance Manager
*CMMS – Computerised Maintenance Management System. *MSDS – Material Safety Data Sheet.
We (Accendo Reliability) published this article with the kind permission of Feed Forward Publishing, a subsidiary of BIN95.com
Web: trade-school.education
E-mail: info@trade-school.education
If you found this interesting you may like the ebook Bulk Materials Handling Introduction.
Leave a Reply