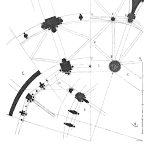
Interpreting Standard Testing Results
Speaker: Fred Schenkelberg
When you ‘pass’ a standard based test, just what does that mean? How can you use test results in a meaningful way other than just noting the product ‘passed’? Understanding the failure mechanisms at play along with the statistics is key.
Military standards, GEIA, IEEE, ANSI, etc provide detailed test procedures for a wide variety of situations. I have yet to find a standard test procedure that details what specific materials and failure mechanisms the test is applicable. One might exist, I’ve just missed it.
Just because 7 prototypes survived 168 hours of 85%RH at 85°C and thus ‘passed’ the test, does that mean anything useful as we attempt to determine if our product is reliable or not? Of course, if one or more prototype fails and we don’t ‘pass’ the test, what does that mean? What have we learned from such testing?
Let’s explore the use of testing based on a standard. Sure, it often is required by customers and commonplace in our industries, so let’s understand what passing/failing actually suggest about our reliability. Also, when purchasing a piece of equipment and it lists 15 standards that it meets, here are a few questions to ask about that testing.
All standards are flawed, some are useful (to restated a popular phrase about modeling). Let’s sort out how to glean the useful elements and avoid the pitfalls. The use of standards facilitates communication between organizations. It is only useful if all concerned fully understand the meaning of the results.
This Accendo Reliability webinar originally broadcast on 12 November 2019.
The audio track is now an Accendo Reliability Webinar Series podcast episode. View the episode show notes to listen or subscribe to podcast
Please login with your site registration to view the video recording.
If you haven’t registered, it’s free and takes only a moment.
Dear Mr.Fred,
If you dont mind, I have one question about env testing 85oC/85%. Can you please tell me the reason why in Standard, they alway choose humid=85% and temp=85oC for testing, why not 80oC/80% or 90oC/90%.
I’m sorry if It’s a stupid question .
Tks
Brg
Hi Trinh, Good observation and question. The short answer is 85/85 is achievable with typical or common temp/humidity chambers.
A longer answer is the early work on encapsulated electronic parts did a series of tests to evaluate the ability of the epoxy to seal properly around the protruding metal leads. They found that evaluating parts for a fixed time at 85/85 was sufficient to determine if the seal was adequate or not.
Eventually, this testing became a standard for evaluating electronic parts, specifically how well the encapsulate seals. That standard became a ‘standard’ for other failure mechanisms that could be accelerated or detected by using temperature and humidity. In some cases, the new tests have supporting characterization work, while many do not.
As with any test standard, it is wise to question the connection between the test conditions and what specific failure mechanisms are involved. Most standards for testing do us no service by not being specific about what the test is for and its limitations.
thanks for asking
cheers,
Fred
Dear Mr.Fred,
Thank you so much for your detailed answer.
Brg
trang