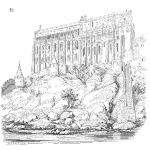
The other day I got a question about the difference between ALT and HALT. There was some confusion probably because of the similar words in the acronym. ALT is Accelerated Life Test, and HALT is Highly Accelerated Life Test.
One would assume that HALT is a faster version of ALT, which it is not in most cases.
ALT is characterized by testing the unit above expected stress levels or more often and above specification levels in order to create the failure mechanisms that would have occurred eventually at nominal stress levels. This is done using one stress parameter, yet could use multiple stresses.
HALT could be called a discovery evaluation. The testing is also above specification limits and may include multiple stresses at the same time. The intent is to continue to step up the stress to cause failures. In other words, to discover the difference between the specification limits and performance limits (or destruct limits – when if fails such that it doesn’t recover).
ALT answers the question, when will the unit fail. HALT addresses what will fail, or how much margin exists within the design.
ALT can be as simple as increasing the occurrence of some function, say a car door. If one expected (maybe observed or measured with existing cars) that the driver’s door will experience four open/close cycles per day on average, then simply opening and closing the door more often per day would be a simple way to accelerate failure mechanisms related to the open/close cycle.
There are many models that relate the effect of the stress applied to the failure rate or expected life distribution. For example, the Arrhenius model relates temperature to the rate of a chemical reaction, say corrosion. The activation energy value is specific to the specific failure mechanism and should be chosen with care.
Using a model permits the design of an ALT that uses only one stress condition and relies on the model to translate the testing results to use conditions. Other ALT approaches include step stress and degradation. In most cases, careful design of the ALT includes understanding the failure mechanisms and statistics.
HALT is the exploration of the stress on the product’s performance with the intent to quickly identify the weakest elements of the design. The use of multiple stresses and relatively rapid step increases in one or more of the stresses makes modeling the effects very difficult if not impossible to model.
HALT is good at finding weaknesses in a design or the assembly process. HALT discovers areas that insufficient margin and are more likely to fail given normal material and use variations. HALT is also typically down with only a few units for testing, often not more than four units.
HALT is also relatively quickly accomplished relative to ALT. HALT may take a day to a week to accomplish, depending on size and complexity of the product. Whereas, ALT may take a day to months to accomplish mostly depending on the ability to accelerate the failure mechanism in a meaningful manner.
ALT and HALT are two types of tools available to reliability professionals. While three of the letters in the name are shared, they are quite different and serve us in different ways. I heard the other day that HALT precipitates failures, and ALT predicts failures. That may be a useful way to keep the two definitions separate.
We will explore more about HALT and ALT in other posts, yet if you have any questions, please leave a comment. Or, just let us know how you have found an easy to understand the way to explain the difference between HALT and ALT.
Related:
Discovery Testing (article)
Reliability Management Terminology (article)
Program Elements Part 2 (article)
Hi is HAST is same as ALT?
HI Reddappa,
HAST is commonly meant highly accelerated stress test, which could be an ALT, accelerated life test. The difference is in the intent. If the HAST is to find defects or failures quickly, often by using multiple high stresses at once, then it is not an ALT. ALT’s almost always focus on one failure mechanism and the experiment or test is to determine the life distribution or minimum time to failure.
Of course if that is the purpose of the HAST then they are the same.
In reliability engineering we have many terms and abbreviations – and not a fixed set of definitions.
cheers,
Fred
Thanks a lot…
I was always puzzled by the assumption that activation energy of electronic devices is taken as 0.7ev. Is there any basis to that assumption. If it related to any particular failure mode what is that failure mode. what is the most frequent failure mode in electronic devices and what is its activation energy. Also I observe reliability engineers tend to associate activation energy to type of product ( electrical , mechanic, or electro-mechanical) instead of type of failure mode. How can this be explained.Can you please clarify my question. Incase these questions have already been discussed please post link to the article. Thanks in advance..
Hi Reddappa,
Activation energy is from chemistry and unfortunately is not easy to determine in all cases. Also the formula for rate reaction seems to describe the change if failure rate with time in many cases.
Be careful when using activation energy. Is it known for the chemical reaction involved in the failure or is simply another fitted parameter.
See a longer discussion at
http://nomtbf.com/2012/05/arrhenius-or-erroneous/
cheers,
Fred
I was here to check out HALT, but saw your discussion on 0.7eV Ea. I was in a semiconductor company as a reliability engineer before, Ea of different value in fact have different physics behind.I have done some experiments which also showed that similar degradation mechanism have similar Ea value. I would like recommend a paper “http://www.intersil.com/content/dam/Intersil/quality/rel/calculation_of_semiconductor_failure_rates.pdf”.
As can be seen from the paper, some defects related failure are 0.7eV but not every failure mode. 0.7eV is widely used now as a history issue 🙂 or based on the assumption that failures mostly come from defects.
Hi Lanfei,
thanks for the note and link to the article. Unfortunately it is too common that people grab the 0.7eV or other activation energy without thinking though the connection to the failure mechanism in question.
Cheers,
Fred
Hello Fred,
Thanks for this useful article.
I am an engineering student and I was wondering if you could advise, if there are any IEC standards in which the ALT test is mentioned.
Thanks in advance,
Sonja
Hi Sonja,
I’m sure there are a few. I went to iec.ch and did a site search
https://www.iec.ch/search/?q=accelerated%20life%20test
I wanted to check as I’ve not used any IEC standards for ALT – as the few I’ve seen over the years do not convey the specifics of the failure mechanism under evaluation and enough details concerning the acceleration factor relationships. Some ALTs found in standards are useful, yet I advise caution in their use unless you fully understand the relationship between stress and the accelerated failure mechanism(s).
Cheers,
Fred
Thank you!