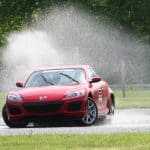
Happy New Year! And thank you for letting us break your stuff to improve your design in 2018. This is a story of when I was NOT invited to break things but did anyway.
Your Reliability Engineering Professional Development Site
All articles listed in reverse chronological order.
by Adam Bahret Leave a Comment
Happy New Year! And thank you for letting us break your stuff to improve your design in 2018. This is a story of when I was NOT invited to break things but did anyway.
by Perry Parendo Leave a Comment
There are many benefits from acquiring our services. But what if you do not bring us in? This anti-case study describes a situation where they wanted to wait. The impacts came from discussions with company employees after the changes. Can you really afford to wait? [Read more…]
by Doug Plucknette Leave a Comment
In continuing this year’s theme regarding common questions on relevant topics, today I have the 5 most common questions people have been asking me about the Industrial Internet of Things. Like every other article or Blog I have posted in the past I encourage you to all to jump into the conversation by asking questions or providing comments to my questions and answers. [Read more…]
Guest post by Msc Teofilo Cortizo
The term MTBF (Mean Time Between Failures) within maintenance management, it is the most important KPI after Physical Availability. Unlike MTTF (Mean Time To Failure), which relates directly to available equipment time, MTBF also adds up the time spent inside a repair. That is, it starts its count from a certain failure and only stops its counter when this fault was remedied, started and repeated itself again. According to ISO 12849: 2013, this indicator can only be used for repairable equipment, and MTTF is the equivalent of non-repairable equipment.
The graphic below illustrates these occurrences:
Calculating the MTBF in the Figure 01, we have added the times T1 and T2 and divided by two. That is, the average of all times between one failure and another and its return is calculated. It is, therefore, a simple arithmetical calculation. But what does it mean?
Generally speaking, this indicator is associated with a reliability quality of assets or asset systems, and may even reach a repairable item, although it is rarer to have data available to that detail. Maintenance managers set some benchmark numbers and track performance on a chart over time. In general, the higher the MTBF the better, or fewer times of breaks and repairs over the analyzed period.
Once we have fixed the concepts, some particularities need to be answered:
1. Can we establish periodicity of a maintenance plan based on MTBF time?
2. Can I calculate my failure rates based on my MTBF?
3. Can I calculate my probability of failure based on my MTBF?
4. If the MTBF of my asset or system is 200 hours, after that time will it fail?
It is interesting to answer these questions separately:
The MTBF is an average number calculated from a set of values. That is, these values can be grouped into a histogram to generate a data distribution where the average value is its MTBF, or the average of the data. Imagine that this distribution follows the Gaussian law and we have a Normal curve that was modeled based on the failure data. The chart below shows that the MTBF is positioned in the middle of the chart.
In a modeled PDF curve (Probability Density of Failure) the mean value, or the MTBF, will occur after 50% of the failure frequencies have occurred. If we implement the preventive plan with a frequency equal to the MTBF time, it will already have a 50% probability of failing. Therefore, the MTBF is not a number that indicates the optimal time for a scheduled intervention.
Considering the modeling of the failure data to calculate the MTBF, it´s only possible in the exponential distribution fix a value where the failure rate is the inverse of the MTBF:
MTBF = 1 / ʎ
In this distribution, the MTBF time already corresponds to 63.2% probability of failure.
Any modeling other than exponential, the failure rate will be variable and time dependent, so its calculation will also depend on factors such as the probability density function f(t) and the reliability function R(t).
ʎ(t) = h(t) = f(t) / R(t)
Although the exponential distribution is the most adopted in reliability projects, which would generate a constant failure rate over time, most of the assets have variations within their “bathtub curve”, as exemplified by Moubray:
This means that the exponential expression is not best suited to reflect the behavior of most assets in an industrial plant.
As seen above, only in the exponential distribution has a constant failure rate that can be calculated as the inverse of the MTBF. In this case, yes, we can calculate the probability of failure of an asset using the formula below:
f(t) = ʎˑexp(-ʎt)
For other models where the failure rate depends on the time, it is only possible to calculate the probability of failure through a data modeling and determination of a parametric statistical curve.
The question is, what exactly does that number mean? It was shown that MTBF isn´t used as a maintenance plan frequency. According to the items explained above, this time means nothing as it is not comparable to its history over the months. If the parametric model governing the behavior of the assets in a reliability study is not determined, the time of 200 hours has no meaning for a probability of failure. In the case of the MTBF provided by equipment manufacturers is different, through life tests they determine exponential curves and thus calculate the time in which there will be 63.2% of sample failures.
I hope the article has helped us to reflect on the definitions of an indicator that is both used but also so misunderstood within industrial maintenance management.
Msc Teofilo Cortizo
Reliability Engineer
by Greg Hutchins Leave a Comment
Guest Post by James Kline (first posted on CERM ® RISK INSIGHTS – reposted here with permission)
In November 2018, the U.S. Global Change Research Program issued Volume II of the Fourth National Climate Assessment Report. Volume I was issued in 2017. It deals with the science behind global change. Volume II deals with the impact of global warming on natural environment, agriculture, energy production, human welfare, and societal impact. This article discusses the assessments made in Volume II. [Read more…]
by Carl S. Carlson Leave a Comment
Before commencing with the FMEA meetings, it is essential to visibly show the nature and scope of the analysis. This article discusses different ways FMEA scope can be made visible, and why this is a necessary step.
“The soul cannot think without a picture” – Aristotle
The electrical conductivity (and its opposite, resistivity) of water based solutions indicate its electrical current carrying ability. High conductivity occurs when many charged atoms and ions are in the water. This typically means the presence of dissolved metals, salts, acidic or alkali chemicals. Conductivity probes are used to measure the total level of charged particles present. This article explains how conductivity probes work and their application in boiler water treatment and management. [Read more…]
by Dennis Craggs Leave a Comment
Statistical Process Controls (SPC) is a suite of methods that can be employed to control a manufacturing or assembly process. It has a wide range of potential applications ranging from consumer products to defense. It can be employed at the lowest element of component manufacturing or an assembly operation.
This article discusses the assumptions necessary to understand SPC.
by Perry Parendo Leave a Comment
Many times, new equipment does not move smoothly onto the production floor. Eventually, operations will say “just get it out here.” Using our methodology, we have helped companies be in a position where they are telling us to wait to install it! When you can understand the equipment up front, it makes a huge impact. How do you fit on the spectrum? [Read more…]
When is the best time to do an RCM analysis on your equipment?
While RCM Blitz™ can be applied at any time in the asset lifecycle, the best time to do an RCM analysis is in the design phase of a capital project. Reliability Centered Design is much more than a thorough RCM analysis on a critical asset, it also uses [Read more…]
by Robert Allen Leave a Comment
Tasks (or action items) are a fundamental building block of an ongoing work-effort or project schedule. While we tend to think of completed actions as deliverables, a project schedule can also be considered a project deliverable….and the value of well-written task (within the schedule or otherwise) is often overlooked.
Generally, a task begins with a verb (some action to be performed) to achieve a milestone or outcome to some desired level of completion. (Recall a previous related article where we discussed the “definition of done”.)
by Greg Hutchins Leave a Comment
Guest Post by Geary Sikich (first posted on CERM ® RISK INSIGHTS – reposted here with permission)
The BP Deepwater Horizon catastrophe cast a shadow on the oil industry and its senior executives. Has the industry learned its lessons or will it be forced to repeat the same mistakes over and over again? Oil company executives and board members should have seen the Deepwater Horizon event is as a wake-up call for the industry. [Read more…]
A spinning pump impeller provides the means to draw incoming product through the pump, energise it, and then force it out under pressure. The impeller coverts the electrical energy from the motor into hydraulic energy of the liquid. It does this by taking the liquid into the center of the impeller and flinging it outward at high speed. To efficiently continue to do this the impeller must remain in the same condition as it was when first installed. If the impeller deteriorates the conversion from electrical to hydraulic energy becomes inefficient. Power is wasted, flow and pressure fall and the pump cannot do its designed duty. [Read more…]
by Christopher Jackson Leave a Comment
Before you go on, please have a look at British comedian John Oliver’s video on infrastructure – https://www.youtube.com/watch?v=Wpzvaqypav8.
OK, if you are reading this and still haven’t watched the video … please go back and try again. You can do it.
If you haven’t watched the video by now, then I concede defeat. In short, the video is a humorous take on the state of US infrastructure. Particularly bridges. Bridges have been collapsing with alarming frequency in recent years. And after much political wrangling there is still no plan to pay for fixing crumbling columns, spans and struts. It is not as if the federal and state governments don’t know how bad things are (again … watch the video).
Oliver proposes a perhaps novel reason for all of this. [Read more…]
by Dennis Craggs Leave a Comment
Quality Costs for manufacturing or services can be categorized as prevention and appraisal costs, and internal and external failure costs. Control occur in prevention and appraisal activities, both of which rely on data. However, when data is collected, it shows variation. One must understand variation to know how to react.
Dr. Deming indicated that 94% of variation is from common causes and about 6% is from special causes. So what are the common and special causes of variation?
[Read more…]