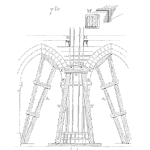
Is your scrubbing tower working? A wet scrubbing tower is used to clean odors, particles, mists and vapours from a gas stream. The gas is forced through the tower. As it moves from inlet to outlet it is washed and cleaned. The washing is done with suitable chemicals that remove the active components in the gas flow. The gas is cleaned to environmentally acceptable levels and discharged to atmosphere. Keywords: packed tower, packing, fill, mist eliminator. [Read more…]