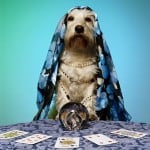
Weibull analysis is a tool that is used for characterizing the behavior of a data set. The value of characterizing a data set is being able to make predictions of failure rate for the same or a similar population. Input to the Weibull analysis is time to fail for all failed units and running time for operating units. The assumptions for the data set are critical to ensuring the right information is included in the analysis. This may include root cause analysis of the failures so they can be characterized as wear-out or use stress related. It would be beneficial to separate these two data sets because their characterization and behavior will be quite different Weibull factors. [Read more…]