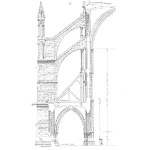
In the previous article, What is Reliability Optimization, we defined the concept. One of the elements of optimization is identifying which elements of a system to focus improvement efforts on.
Simply improving every element of a design may provide an overall improvement of reliability performance.
Given constraints such as time or funding, selecting the specific few elements that would provide the most improvement is key. [Read more…]