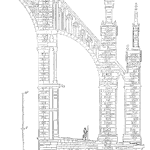
It is rare that a third party generated FMEA/FMECA has any value. The development or manufacturing teams and supporting staff should comprise the bulk of the study’s team. Team size for a specific study would include 4 to 10 individuals.
The FMEA/FMECA should provide clear action items that may include:
Conduct research or experiments to understand and quantify uncertainty. This may include exploring how an item responds to specific stress, errors or inputs. Or include experiments to estimate the occurrence rating for a specific potential cause of a failure mode. [Read more…]