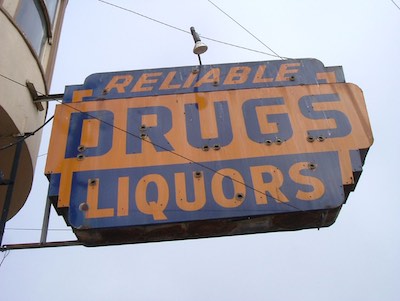
Supplier Reliability Information Requests
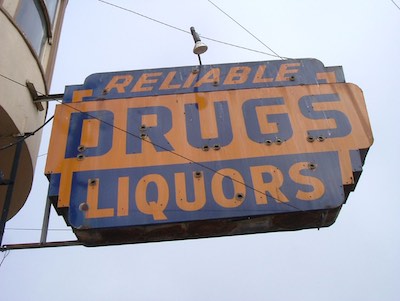
Every now and then we need to ask a supplier for a reliability estimate for a component they produce. Our team may be considering adding the part to a system and would like to know if it is reliable enough to meet our needs.
The request for reliability information is often along with requests for features, functions, quantity delivery capacity, costs, lead times, and many other elements of information needed to determine if the purchase is appropriate. The reliability question may not be the most important, or it may be a deciding factor.
We receive an MTBF value. In one specific request concerning a cooling fan, they told use the fan’s reliability is 50,000 hours.
Initial Reaction
“They must be idiots” was my first reaction and may have even said it out loud.
Very few components actually have a constant hazard rate. Very few components follow the ‘flat part’ of the bathtub curve and may be described with an exponential distribution. Very few components have an insignificant early life failure period or total lack of a wear out period.
After taking a few deep breaths, as my boss suggested (urged), before picking up the phone to call the procurement manager in charge of discussions with the vendor, I gathered my thoughts and wondered how to confront the procurement manager and the vendor. We wanted actually and useful reliability information, not MTBF.
Something was missing or lacking from the request or the response.
Considered Reaction
With “probability shouldn’t call them idiots” still fresh in my mind (advice from my boss as he left me to respond), I took a few more deep breaths. What could I say that would help us receive the necessary reliability information from the vendor.
Their may two problems at play. First, the procurement team doesn’t know how to ask for reliability information and may not understand how we use the information to answer specific questions. And, second, the vendor may or may not know how to provide the requested reliability information.
Procurement’s Request
The request for reliability information was probability part of a larger discussion and may have been as simple as, “please send over reliability information for widget xyz”, or “how reliable is the widget”. The request may have been written yet not very specific on the expectations or use concerning ’the reliability information’.
The procurement team is only passing along the request from engineering and most likely is not going to use the reliability information directly for the decision to work with the vendor or not. Reliability information is probably not something they know how to use to judge the worthiness of a component.
In most cases they may use the reliability claims from various vendors to compare claims. A higher duration in the claim is better, right? Thus a high MTBF claim implies a more reliable component. Given a rough idea of the system’s expected reliability (it’s rare that teams break down the reliability requirements to individual components, much less share it with the procurement team) the procurement manager may consider a 50,0000 hour figure as more than adequate given we only offer a one year warranty.
Vendor’s Response
Any manufacturer may receive multiple requests for reliability information every day. In most cases it is probably bundled with many other requests that range from specifications to weight to delivery schedules. Occasionally, maybe too rarely, they receive a very specific request concerning reliability, most likely prompted by a spat of component failures.
The vendor provided MTBF because quite a few customers specifically ask for the MTBF (meaning reliability) for the component. Plus, when providing MTBF for other customers, they do not ask for anything else and seem good with that information. It’s quick, easy, and seems to be the appropriate response to requests for reliability.
Providing MTBF in response to a reliability request does not indicate if the vendor knows very little or quite a bit about the actual reliability performance of the component. With a fan for example they may fully understand the relationships between temperature, use, load, etc., and time to failure distributions for the lubrication failures and eventual bearing failures, plus may understand a dozen more potential failure mechanisms in detail.
Or they may not.
It’s hard to tell when all they provide is 50,000 hour MTBF.
Better Questions to Ask
When, after many more deep breaths given my volatility concerning MTBF, I sit down with the procurement manager I have a very short agenda. First, let’s discuss how we plan to use the reliability information to determine if the component is appropriate for the system. Second, let’s discuss a couple of questions to ask the vendor that may help us receive the appropriate reliability information.
On the design team we are interested in the component reliability with a specific reliability capability. There are four elements of concern. The function(s) – meaning what does the component do and it should provide these functions over time. The environment – inside the system the temperature is 15°C higher than ambient air, there is a back pressure load, there is dust, moisture, humidity, vibration and power supply variations. The component needs to work over time in this specific environment. The probability of successful operation over time – the reliability (probability of success) has to meet or exceed the apportioned target at these specific durations of early life, warranty of design life.
We are interested in the specific failure mechanisms most likely to occur. We use this information in our risk analysis (FMEA and Hazard’s analysis studies), plus in testing to monitor expected behavior and enable detection of anomalous behavior.
We are interested in the lifetime distribution and how that distribution changes for different stresses, plus an understanding the relationship between stress and time to failure so we can consider a range of tradeoffs that impact the reliability of the overall system and the component.
So, this narrows down to a couple of questions.
- What is the time to failure distribution for the component? How is this determined (evidence)?
- What are the expected failure mechanisms given our use environment and design? Or, in general what are the expected or most likely failure mechanisms (details on what fails and why)?
- What can we do to minimize component failures in our design? Why? What are the relationships between stress and time to failure?
If the vendor is unable or unwilling to answer these questions, it may be time to consider other suppliers. Maybe this particular team doesn’t really understand their product very well.
If they can provide this information, or are willing and need some help articulating the information, it’s evidence that they do understand their product and have an interest in reliability.
In my experience most vendors design and manufacture components that they, like us, want to work as expected over time and provide value. They have a range of experience and capabilities, yet few totally ignore reliability. By asking better questions we can help our vendor provide better information.
If you supply components or respond to reliability questions, don’t wait for the better questions, provide better answers. Help you customers appreciate your reliability knowledge and help your customers make better decisions concerning reliability.
Excellent article! Congratulations! Thanks for your efforts to spread the reliability knowledge among us!.
Hi Marcelo,
Thanks for the kind words. Glad to help and share what I know. Always learn in the process and look forward to any additional insights or ideas.
Cheers,
Fred
Well written. Yes, the answer boils down to the three questions: Failure distribution, Failure Mechanisms, and Systematic control of contributors to the mechanisms.
For new designs and one-off designs failure distributions are not practical, thus the physics-of-failure is the only tool to get to higher reliability – understand the failure mechanisms and effectively control the contributing factors.
MTBF / MTTF numbers are required to estimate logistical issues when dealing with large quantities such as with electronic components and in the military. They have their place, but most often over used and misused.
Hi Rakesh,
Thanks for the kind words, much appreciated.
I agree with your points except the role MTBF/MTTF has with logistical issues – beyond being misunderstood the use of MTBF and the like leads to massive waste and very poor logistical planning. Much better to use the distributions directly and we have the tools and computing power so using MTBF or average failure rate is really not an excuse.
Sorry, I really find MTBF wanting especially with respect to logistics.
Cheers,
Fred
Dear Fred,
I appreciate your efforts for writing such an amazing articles in reliability field, which is very helpful for many reliability professionals all over the world. In this article you have very well written about how to deal with vendor for obtaining reliability information but it is not easy to deal with.
It’s not easy to get the reliability information from vendors (atleast not from many). If we ask for the particularities like failure distribution, failure mechanisms, operating limits/loads, etc, they would have mostly not carried our these studies or may not have think that these metrics are important.
Some would cleverly reply saying, ‘we can provide you all the information provided you choose us to be your supplier’ which is rather stupid and some would amazingly reply ‘sorry we cannot provide this information as this is very confidential and you gotta sign a contract with us such that we can provide you this information’ on the contrary I believe that they haven’t carried out such studies.
There are also some vendors who might not have carried out these studies but would be interested to do, as they might have the thorough knowledge of their product/system and may need some guidance how to accurately get such information and all such vendors would rather be goal oriented rather than money oriented.
So over and out, just FMEA sheets (with brief failure causes, effects and the control actions), HAZOP, rough MTBF values provided by the vendors may not be of help, but they could be verified (one should evaluate vendor’s information) and used as an useful information to decide the vendor/supplier, on the other hand in such evaluations they cannot misuse the MTBF or MTTF (for electrical, mechanical or electro-mechanical products) or FMEA sheets, thus leading the vendor to obtain the required reliability information.
P.S: Keep writing such articles and keep inspiring us (Reliability Professionals from all over the world).
Cheers,
Douzi Imran Khan.
Hi Douzi,
Thanks for the thoughtful comment. Yes asking and getting good reliability information is difficult, yet by not asking we’ll be sure to not get the information.
Cheers,
Fred