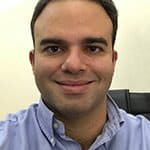
Guest Post By: Luis Daniel Khalil
Condition monitoring can help to predict failures and anticipate to them, however it doesn’t always work like this — in the best case scenario we might be able to identify early phase failures or incipient stage of damage mechanisms or failure mechanisms, but if we use it in the wrong manner it will just be a reactive tool.
More than 80% of the failure modes could be randomly patterned. Although performance, vibration, temperature or lube oil condition are being monitored, many of the failures are still not directly predicted by only these conditions.
It is good to highlight that those failures during wear out phase would be highly probable to predict and identify incipient stage failure, isolate a failure mechanism, and to monitor it using condition monitoring analysis combined with highly skilled people.
For example in a Gas Turbine, the failure mechanism: vane corrosion could be feasible to be identified by performance drops during monitoring. Vibration patterns would also be shown as symptoms, and after that we could combine with boroscopic inspection (when feasible, like for aero-derivatives ones).
Finally, this failure as a wear out pattern could be monitored, isolated, predicted, and the overhaul planned in an efficient and cost-saving manner (avoidance of production losses, safety impact, and optimal intervention costs.)
Rotordynamics are important to troubleshoot a turbomachine, vibration patterns showing whirling, oil whip (critical speed cases), or bearing loads. With skilled interpreters it can provide practical advice for unstable machines.
However, to improve plant availability, safety, and reliability, we are required to address these failure modes coming in the form of random damage mechanisms.
We must act in a timely manner, even before the failure develops.
Root Cause Analysis, properly done, can identify that the main reasons of these conditions are operating upsets or process changes.
Only to mention some: change in gas molecular weight, atmospheric condition changes, liquid / salt / chemical carry over equipment, CO2 in water concentration, low-level suction tanks, oil preservation, increased speed of rotation, low suction flow, higher suction temperature, upset in utilities like instrument air, fuels, water treatment, and many more.
Definitively one must look at the most probable and critical causes of these 80%.
Based on experience in refineries and oil/gas facilities, the main sources of these random failures often come from process and/or operational upsets- changes in operating conditions.
How does this happen?
Something is happening during the productive and manufacturing processes- variables are changing in time- they increase and decrease, they go up and down, and nothing is perfectly stable. When the process variables and operating conditions go outside certain ranges, (upper and/or lower limits) the assets will feel this change.
It may not be immediately felt, however after certain quantities of times to exceed minimum or maximum values, the assets might be showing certain changes of their conditions, like vibration, temperature, or even corrosion rate in static equipment.
These would increase beyond the normal or expected values or rates. All these operational and process changes shall be identified, categorized, prioritized and even monitored to trigger a special inspection plan or condition-monitoring customized frequency in the loop, system, or specific equipment or machinery.
This special inspection goes outside the normal or fixed frequency, thus the incipient failure could be or would be identified. After this incipient condition is identified, it’s time to act.
Set the conditions in the process to steady or normal range as soon as possible and as feasibly as possible. Additionally, in parallel one must act immediately to increase the monitoring or inspection frequency until intervention can take place in a safe, pre-planned, and efficient way.
Raise the flag to stop and fix before the failure becomes unacceptable (based on equipment design, standards and risk management.)
What we want is this: Plan Do Act, asset management, risk management, reliability engineering, process engineering, operational reliability, human reliability, technical and operational teams, SME, technical authorities, decision process, Industrial Internet of Things, technology, automation, control, tools, and digital signals working together with the same objectives, vision and languages.
Proper RCMs combined with highly skilled people in troubleshooting and “Inductive Root Cause Analysis ®” will help to identify Asset Health Care Plans for machinery and critical rotating equipment. API 571, API 581, and NACE best practices and new cases with a highly skilled operational committee (corrosion engineers, process engineers, operators, asset integrity team) would help to prepare corrosion loop special plans for static equipment, piping and pipelines.
Let’s work on it.
Leave a Reply