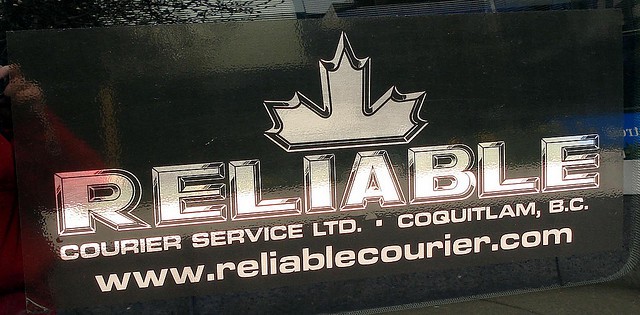
What do we know with MTBF

Reliable
How many times have you been given only MTBF, a single value? The data sheet or sales representative or website provides only MTBF and nothing more. We see it all the time, right? It is provided as the total answer to “what is the reliability performance expectation?”
So, given MTBF what do we really know about reliability?
As you may suspect, not much. [Read more…]