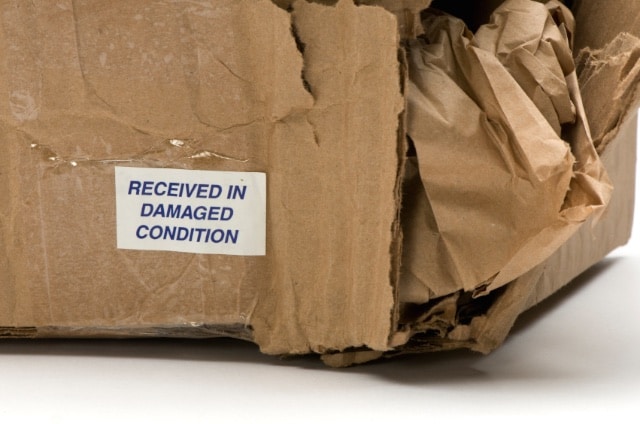
Establishing a Reliability Goal
The basic question of ‘How long should it last?” may be the first question you consider related to reliability of your product or production equipment. Ideally we would like to create a product that will never fail for our customers, or a set of equipment that just keeps running. [Read more…]