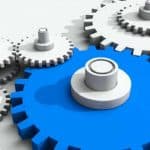
Any maintenance manager at a manufacturing plant or facility is likely aware of the problems caused by faulty equipment. Even if just one piece of equipment out of thousands breaks down, it could cause your entire operation to come to a halt. Preventive maintenance involves scheduling various maintenance activities to keep your equipment in peak condition and prevent breakdowns and failure. EAM/CMMS software is an essential tool for scheduling preventive maintenance and monitoring performance. The following are 5 tips to improve preventive maintenance with maintenance management software.