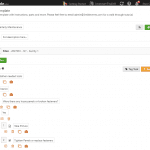
Equipment maintenance is a requisite for companies that seek high-performance from their physical assets. If they can leverage a well-executed maintenance strategy, such organizations should gain the expected advantages that reliable assets will deliver such as reductions in operational costs and unplanned shutdowns.