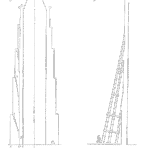
When people first begin to learn about Reliability Centered Maintenance and methodologies like RCM Blitz, they get excited about the potential results that can come from performing a RCM analysis and implementing the resulting tasks. Shortly after completing their RCM Training some begin to understand that good RCM takes leadership, structure and discipline, others begin to think of ways to shortcut the process. [Read more…]