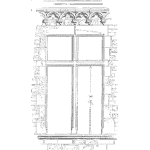
Maintenance Data Integration with Kevin Clark
Abstract
Kevin Clark and Fred discussing a new set of devices and services to provide real-time vibration and temperature data for your factory’s assets.
ᐅ Play Episode
Your Reliability Engineering Professional Development Site
Author of <a href="/creprep/">CRE Preparation Notes</a>, <a href="/on-product-reliability/musings">Musings</a>, <a href="/articles/nomtbf/">NoMTBF</a>, <a href="/book-author/fred-schenkelberg/">multiple books & ebooks</a>, co-host on <a href="/series/sor/">Speaking of Reliability</a>, and speaker in the <a href="/series/sor/">Accendo Reliability Webinar Series</a>.
This author's archive lists contributions of articles and episodes.
by Fred Schenkelberg Leave a Comment
Kevin Clark and Fred discussing a new set of devices and services to provide real-time vibration and temperature data for your factory’s assets.
ᐅ Play Episode
by Fred Schenkelberg Leave a Comment
If your product is stronger than the applied stress, it should work. The concept of the stress/strength relationship is well known, yet did you know both stress and strength change over time? Let’s use the best information and tools for this analysis. [Read more…]
by Fred Schenkelberg Leave a Comment
Product failures occur due to the material or component variability. The steel in a bracket is more brittle then optimal, or the capacitance is on the low side of an acceptable range. Designing a product with variation in mind enables the creation of a reliable product. [Read more…]
by Fred Schenkelberg Leave a Comment
On this week’s episode of Rob’s Reliability Project, I sit down with James Kovacevic and talk about preventive maintenance optimizations (PMOs). James helps us understand what a PMO is, how we can do it better and gives us some tips on what to avoid.
Follow James Kovacevic on LinkedIn at:www.linkedin.com/in/jameskovacevic/
Follow Rob Kalwarowsky on LinkedIn at:www.linkedin.com/in/robert-kalwarowsky-p-eng-03a43552/
For any questions or inquiries, emailrobsreliabilityproject@gmail.com
by Fred Schenkelberg 4 Comments
Stress screening, highly accelerated stress screening, burn-in, are expensive activities and to be avoided. Yet stress screening does have a valuable purpose in specific circumstances. Let’s talk about when and why you may conduct stress screening.
[Read more…]
by Fred Schenkelberg 2 Comments
The Friedman test is a non-parametric test used to test for differences between groups when the dependent variable is at least ordinal (could be continuous). The Friedman test is the non-parametric alternative to the one-way ANOVA with repeated measures (or the complete block design and a special case of the Durbin test). If the data is significantly different than normally distributed this becomes the preferred test over using an ANOVA.
The test procedure ranks each row (block) together, then considers the values of ranks by columns. The data is organized in to a matrix with B rows (blocks) and T columns (treatments) with a single operation in each cell of the matrix. [Read more…]
by Fred Schenkelberg 1 Comment
Systems and processes exist in our dynamic world. Each organization and situation is different. Just as there is not one risk management process that works for any organization, there also is the need for continuous improvement of an existing system.
When first designing a risk management process for your organization, you consider your objectives and adjust a framework to fit your needs. Over time your objectives and the surrounding environment changes, thus requiring a critical look at your process. [Read more…]
by Fred Schenkelberg Leave a Comment
An element of a complete reliability goal statement involves a product’s environment and use conditions. The ability to define these clearly during the design process is not always easy yet a valuable addition to your reliability program.
[Read more…]
by Fred Schenkelberg Leave a Comment
A common question about reliability testing is “what is the sample size?” It is also a difficult question to answer well. The right sample size is a balance between cost, accuracy, and variability. In some cases, we also consider the time to results.
[Read more…]
by Fred Schenkelberg 2 Comments
Let’s say you have shipped 1,000 products to your customer on January 1st. All are immediately placed into service. And each month since you have received a few product returns, what we are going to call failures. We also have fitted the data to a Weibull distribution. Then in May, your boss asks you to estimate how many failures to expect in June.
This is a simple example as we’re not shipping units every month, nor changing the product design or assembly process. We also have worked out the fitted Weibull parameters already. That leaves the calculation of how many failures we should expect over the next month. [Read more…]
by Fred Schenkelberg 6 Comments
I like to say Reliability is all of quality over time. Quality professional tend to say reliability is an element of quality. David A. Garvin of the Harvard Business School suggests there are eight dimensions to quality, including reliability.
Either way one relates quality and reliability we need to remember that quality or reliability is not a department, team, the engineering down the hall. Quality and reliability is part of the culture of the organization. It is how we make decisions the impact how the product or service performs for customers. [Read more…]
by Fred Schenkelberg 4 Comments
“How many samples do we need?” is a very common question. It is one you will receive when planning nearly any kind of reliability testing. It is a great question.
Having too few samples means the results are likely not useful to make a decision. Too many samples improve the results, yet does add unnecessary costs. Getting the right sample size is an exercise starting in statistics and ending with a balance of constraints.
There are six elements to consider when estimating sample size. We will use the success testing formula, a life test with no planned failures, to outline the necessary considerations. [Read more…]
by Fred Schenkelberg Leave a Comment
We can plan to do more than we are capable of accomplishing. The remaining items, if they warranty accomplishing become deferred. They roll over to the next’s day’s list of actions to take.
Of course, in practice, the process to plan, execute, and defer maintenance activities is a bit more complex than described above. The ability to maintain equipment in working order along with minimizing downtime and costs is in large part the balance between resources available to conduct maintenance and the increased risk of system failure due to deferred maintenance. [Read more…]
by Fred Schenkelberg Leave a Comment
When looking at a pile of data, sometimes there is a data point that is not like the others. It attracts attention as it is different than the rest of the data.
When I spot something odd in a dataset, I wonder if there is something to learn here. Is this an opportunity to make a discovery or improve a process?
All too often it is tempting to remove the outlier as a mistake. Or to drop the outlier as it doesn’t make any sense and ‘messes up’ the analysis. [Read more…]
by Fred Schenkelberg Leave a Comment
A risk management plan has to meet your organizations needs as the organization identifies, manages, and mitigates potential and actual risks. The ISO 31000 framework does not detail how an organization should plan or what elements are required for an effective plan.
This short article outlines a few details that may comprise a starting point as you build a risk management plan within your organization. Or, the suggestions here may help you review and improve your existing plan. [Read more…]