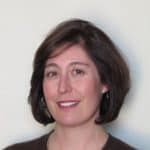
Global Asset Management Certifications with Susan Lubell
We’re excited to have Susan Lubell, the PEMAC Asset Management Association of Canada President, with us. She’s also the chairperson at World Partners in Asset Management and the principal consultant at Steppe Consulting. Susan presents at conferences, instructs, and has been heavily involved in maintenance and reliability and asset management for more than 25 years. These have been in oil and gas as well as mining and mineral processing.
In this episode, we covered:
- What is Asset Management
- Which AM certifications are available
- Difference between CSAMs and CPAMs
- And much more!