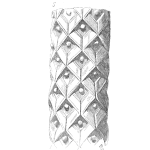
Traditional Predictive Maintenance strategy results in out of control production from random planned equipment outages. A Plant Wellness strategy reduces the need for condition monitoring because you get ahead of failure and eliminate all root causes so there cannot be failure.
[Read more…]