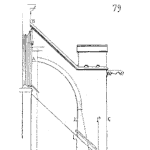
True of False? RCM has serious weaknesses in an industrial environment.
[Read more…]Your Reliability Engineering Professional Development Site
Author of Everyday RCM articles and videos and offers Foundations of RCM course.
This author's archive lists contributions of articles and episodes.
Nancy Regan is a leading authority on Reliability Centered Maintenance (RCM). She has over 20 years’ experience of hands-on practice facilitating RCM analyses, conducting RCM training, and assisting her clients in implementing RCM programs. With RCM, she helps organizations achieve goals such as reducing maintenance costs, identifying the cause of chronic failure, and shifting from a reactive to a proactive maintenance environment. Nancy also helps people overcome the organizational challenges that are in the way of creating an effective Reliability Culture.
by Nancy Regan Leave a Comment
by Nancy Regan Leave a Comment
by Nancy Regan Leave a Comment
Humans are often so focused on the complex, that the simple gets overlooked. Even as technology and our equipment gets more complex, we need to be firmly rooted in the basics of maintenance and reliability.
That’s one reasons why the first step of RCM is so important.
[Read more…]by Nancy Regan Leave a Comment
Should you implement the manufacturer’s recommended maintenance schedules? Not without sanity-checking them first.
Be sure you consider your operating environment, which the manufacturer is unable to do.
[Read more…]by Nancy Regan Leave a Comment
A common step in a RCM program is to conduct a critical analysis to prioritize further analysis of those parts of the system that are critical to the operation. Yet, is criticality analysis required?
No, it is not.
Let’s explore why this may be so for your situation.
[Read more…]by Nancy Regan Leave a Comment
The third step in the RCM process is to identiy failure modes. When a failure mode occurs it leads to a functional failure.
Identifying failure modes correctly and clearly is vital to the RCM process because we manage physical assets at the failure mode level.
[Read more…]by Nancy Regan Leave a Comment
Equipment experts are the untapped gold in any organization.
They know where the vulnerabilities lay, and they know what to do about them. Don’t waste this vital resource.
RCM memorializes the expertise and experience of equipment experts.
[Read more…]by Nancy Regan Leave a Comment
There are two main ingredients for a successful reliability centered maintenance (RCM) analysis:
by Nancy Regan Leave a Comment
Let’s dispel five common myths about reliability centered maintenance, including:
by Nancy Regan Leave a Comment
CBM or Condition-Based Maintenance is a maintenance approach that includes these five facts:
by Nancy Regan Leave a Comment
In this episode, we talk about the more personal (or human) aspect of equipment Reliability. Who is responsible for Reliability? We know the answer is “everyone” – from top management to the experts who operate and maintain our machines. So it’s vital that we understand one another’s perspectives and responsibilities. We discuss how invisible obstacles can personally affect us – Comfort, the Prison of Perfection, Overwhelm, Our Thoughts, The Voices, and Fear. Fear can be the deadliest one of all. In this episode we discuss a simple – yet powerful technique – to manage fear. When we properly manage the obstacles, we free ourselves up to become more productive and effective equipment custodians.
[Read more…]by Nancy Regan Leave a Comment
In this episode, we explore what Condition Based Maintenance (CBM) is (aka On-Condition Maintenance). We’ll talk about : – What CBM is – The biggest trap you can fall into when implementing CBM – And what governs how often you do a Condition Based Maintenance task. As asset managers, we know that most Failure Modes occur randomly, and that can seem a little intimidating or maybe even a little scary, but it doesn’t have to be because that’s where Condition Based Maintenance can be very helpful. The whole point of Condition Based Maintenance is to detect a Potential Failure Condition and take action before failure occurs. That interval is called the P-F Interval and that is explained in this episode.
[Read more…]In this episode, we talk about what preventative maintenance is and what two criteria determine if a preventive maintenance task should be assigned. The biggest pitfall that organizations often fall into when defining intervals for preventative maintenance tasks is revealed.
[Read more…]by Nancy Regan Leave a Comment
In this episode, we talk about what a Failure Mode is and why Failure Modes are so important to equipment Reliability. As responsible custodians, it’s up to us to identify the plausible Failure Modes that could occur so that we can figure out if and how we should manage each one. If we don’t, it can end up in disaster.
[Read more…]by Nancy Regan Leave a Comment
In this episode, we answer two questions: 1) What is Reliability? 2) How do we get the Reliability we need from our machines? Nancy also discusses how we design our Reliability both literally and figuratively. The quality of our proactive maintenance and Default Strategies largely determines the Reliability we get from our equipment. Inherent Reliability is explained.
[Read more…]