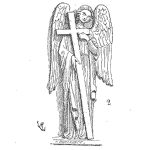
As with strength-strength analysis, derating is a means to design robust systems.
Derating is an intentional process applied to every component of a product to reduce the opportunity of a component witnessing more stress than it is capable of withstanding.
The additional robustness also reduces the amount of damage the stress may impart, thus prolonging the life of the component.
Derating has two approaches.
First, reduce the level of stress applied to the product.
Second, select components that are more robust to the stress.
Stress on electrical components comes in various forms, for derating, there are four types of stress that a derating approach may apply.
- Electrical stress (voltage, current, transients)
- Thermal stress (hot, cold, cyclic)
- Chemical stress (solvents, corrosives, water)
- Mechanical stress (thermal expansion, vibration, shock)
One other method to achieve derating is the reduction of performance stress.
Reducing traffic loading reduces the applied stress due to operating load enable the component or system to operate over a wider range of environmental thermal or electrical stresses.
Reducing the system clock speed, reducing the heat generated, reduces the sensitivity to timing anomalies, etc. again permitting the system to operate in over a broader environmental stress range.
Derating concept
Each electrical component has one or more physical limits.
For example, a capacitor will fail quickly when operated at high temperature or with excessive ripple current which generated internal heating. The heat causes
- distortion or softening of polymer dielectrics,
- damages or delaminates rigid dielectrics thru thermal expansion,
- or hastening the evaporation of wet dielectrics.
Voltage is another stress that commonly causes damage to capacitors. Even normal applied voltage damages the dialectic layer within a capacitor leading to eventual failure.
The higher the applied voltage the quicker the time to failure. Or, with a very high voltage applied relative to the design of the capacitor the component may immediately experience a dielectric breakdown.
Vendors create components that are capable of withstanding specific levels of stress.
The component data sheet will list the maximum applied levels. For example, for a capacitor, they will rate the device with a maximum applied voltage and ambient temperature.
Operating a component at rated values typically will function for a short period of time. The device is at the edge of its ability to function under the applied load. A capacitor rated to operate at 125°C may do so for a few months, and unlikely to operate successfully for a year. Besides temperature, the capacitor role in the circuit, the duty cycle, component assembly variation, and other factors may impact the actual time to failure.
Each component has specific stresses that lead to component failure. Derating guidelines provide a listing of recommended applied stress levels.
Here is the derating information for tantalum capacitor from Kemet:
Voltage Rating | Maximum Recommended Steady State Voltage | Maximum Recommended Transient Voltage (1 ms – 1 μs) |
-55°C to 105°C | ||
12.5 V ≤ VR ≤ 75 V | 80% of VR | VR |
105°C to 125°C | ||
12.5 V ≤ VR ≤ 75 V | 54% of VR | 67% of VR |
The data sheet includes a graphic, too.
It means your selected component is properly derated for both temperature and voltage is the applied stresses fall within the dark blue region.
For example, for this specific capacitor family they are recommending at least an 80% voltage derating for ambient temperatures from -55°C to 105°C. Thus if we select a 35 Vdc rated capacitor, the component should see no more than 0.8 x 35 = 28 Vdc. If our application is nominally a 24 Vdc applied across the capacitor we should be fine.
Derating guidelines often include similar charts depicting the derating information or they simply provide a table of recommendations.
Derating resources
Component vendors often include derating guidelines within the data sheet or as a separate document.
The Kemet derating information above is from KEMET Organic Capacitor (KO-CAP (R) —Industrial, T521 High Voltage Polymer Electrolytic, 12.5 – 75 VDC, accessed 20 July 2016.
The US Navy Derating Guideline, SD-18, is available via the web and besides derating values also provides information about component technologies, testing, and more. SD-18, Part Requirement & Application Guide, NSWC Crane Division, http://www.navsea.navy.mil/Home/Warfare-Centers/NSWC-Crane/Resources/SD-18/, accessed 20 July 2016.
Other readily available derating guidelines include:
- SMC Standard SMC-S-010, US Air Force Space and Missile Systems,
- EEE-INST-002: Instructions for EEE Parts Selection, Screening, Qualification, and Derating, NASA,
- IPC-9592 Performance Parameters for Power Conversion Devices
- Mil-Hdbk-338 Military Handbook Electronic Reliability Design Handbook
Each guideline provides specific guidance for the expected applications. For example, the IPC standard focus on component commonly found in power conversion devices. The NASA and Air Force guidelines expect space-borne or launch equipment.
When I worked at Hewlett-Packard we had an internal derating document focused on consumer and commercial products.
Do you derate? Consistently? If so, which standard do you use?
Another Derating Document: SSP 30312 Revision H, Appendix B: Parts Stress Derating Criteria from the document Electrical, Electronic and Electromechanical (IEEE) and Mechanical Parts Management and Implementation Plan for Space Station Program.
Excellent, thanks Hilaire.
Wasn’t aware of this one.
Cheers,
Fred
Thank you for the opportunity. I am a huge fan of Fred’s work.
Ciprian
When performing a derating analysis is it generally acceptable to use values based on the nominal case circuit analysis, or must worst case values be used. If the latter, that would mean that a derating analysis cannot be performed unless a worst case analysis has been performed first.
Start with calculations based on nominal values. For critical circuits, or those expected to experience a wide range of conditions, then use worst case or close to worst case calculations in order to design a robust system. Another option is to consider using simulation tools and design of experiments to fine tune the circuit design, derating, and performance in a wide range of stress conditions.
Cheers,
Fred
What is the standard derating document about automotive electronic component? Thanks!
Hi Zhenhua,
I’m not sure – maybe check with SAE (society of automotive engineers) as they do have some standards. Another group that does standard related to automotive is AIAG (Automotive Industry Action Group).
In my experience, most companies adopt and further develop their own set of guidelines. This is in part based on lessons learned internally related to internal design practices, suppliers commonly used, etc.
good luck
cheers,
Fred
Hi Fred,
Thank you very much for your reply!
Best Regards!