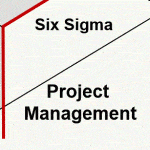
Our previous article covered the benefits of comparing waterfall with agile, emphasizing the benefit of planning the agile process and product backlog content. In this article we’ll compare the Define, Measure, Analyze, Improve and Control (DMAIC) thought process, with a project management thought process.
DMAIC is a problem-solving thought process applies critical thinking to ensure robust problem solving. (See our previous article on the subject here.) DMAIC is not necessarily a process by which projects are managed, however. Recall the high-level project management process as follows:
The key overlapping phases are “measure” (in DMAIC) and “plan” (in simplified project management).
Combining the two would simply include a “Measure and Plan” phase, thereby ensuring a robust problem-solving thought process AND a robust project plan. Recall some of the “plan” phase deliverables that would complement the technical “measure” (of the problem) and business benefit “measure”.
- Project Plan Checklist – a customized checklist that asks key questions about how the project will be managed, executed, monitored & controlled.
- Risk Assessment – an ongoing list of risks, scored by severity x likelihood.
- Action Item List – an ongoing list of actions. Ideally the action item list would include the problem, issue or opportunity, in addition to the corresponding action. Each action has a person responsible and an action sponsor.
- Project Schedule – schedule of activities and milestones, ideally in MS Project. Alternatively, a more informal schedule can be established within the action item list.
- Work Breakdown Structure – define and organize the project work according to a deliverable-oriented breakdown into smaller components (work packages or activities). For DMAIC, the WBS would include deliverables related to the analytical tool or analysis being planned.
In summary:
Therefore, DMAIC can be more effectively executed using a “measure & plan” phase (or at least require planning to be performed in the measure phase). Other benefits include training team members in fundamentals of project management, as well as enabling (planned) deliverables to be reviewed and approved in subsequent gate reviews.
Leave a Reply