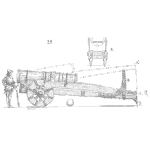
What you will learn from this article.
- The life of a road depends on the vehicle wheel loading.
- Aggregate size determines the strength of the tarmac.
- The sub-base below the tarmac distributes wheel forces.
- Slope the surface to prevent water pooling.
The drawing above shows a typical cross-section through a road and highlights the forces produced by a wheel contacting the surface.
Traffic loads
Heavier loads passing over roadways require deeper and stronger sub-base preparation and a thicker asphalt surface.
Straight flowing car traffic requires bitumen thickness of about 20 mm and a sub-base of 150 – 200 mm whereas trucks would require 30 mm bitumen and a 250 – 300 mm sub-base.
Turning vehicles
A turning wheel causes a side thrust on the surface aggregate in the asphalt.
This tearing thrust has to be transmitted through the top surface and into the underlying sub-base.
The asphalt and sub-base on turns and turning circles are made thicker, about 40 mm, or structurally stronger for this reason.
Top surface thickness
The surface membrane of asphalt must be thick enough to resist turning, braking and impact stresses from traffic.
This is particularly important where there are sharp turns. Consideration of the effects of heavy braking by vehicles may necessitate thickening the asphalt further.
Asphalt aggregate size
Course aggregates lock-in with neighboring aggregate and is less likely to be lifted from the road.
On turning circles, a larger aggregate may be needed than would be required on straight sections.
Sub-base strength
The load carrying capacity and the impact strength of a tarmac surface is proportional to the depth and firmness of the sub-base.
The sub-base supports the tarmac and acts to dissipate forces and spread wheel loads over a wider area. Low structural strength in the sub-base allows it to be overstressed and deform.
This movement is then transmitted through to the top surface which breaks-up.
Sub-base materials
Commonly the sub base is either graded limestone or blended granite aggregate. Each material has different structural properties that affect the depth and construction of the sub-base.
This choice has major cost implications.
Sub-base construction
A strong bond across the interface between the asphalt course and the sub-base is required.
This is achieved by using sub-base materials with a high proportion of aggregate and a low proportion of sand. Excess sand inhibits the development of the bond to withstand the tearing stresses.
In situations with a thin sub-base on a turning circle, the most cost-effective option may be to use 14 mm aggregate bitumen, 65 mm thick, over the existing sub-base rather than rebuilding the entire turning circle.
Underground conditions
Below the sub-base, the ground must be sufficiently compacted, moisture free and void free.
Poor ground conditions several meters below the roadway will eventually cause the surface to fail.
For example, car bodies will have to be removed, buried builder’s rubble prevents proper ground compaction and accumulated water underground causes ‘sponginess’ and requires draining.
Falls and slopes
The tarmac slope must promote easy water runoff.
Pooled water can seep through hairline cracks in the asphalt surface and collect under the tarmac. This water causes separation between the sub-base and the surface layer.
Pooled water can sit between the surface aggregate and produce hydraulic impacts on neighboring aggregate when hit by a fast moving wheel.
The continuous hammering leads to aggregate being popped out of the bitumen surface.
Doing a repair
Before repairing tarmac determine why it failed. At times you may need to get an expert to assist.
Once the investigation is complete decide on how to cost effectively repair the tarmac long-term.
Ensure the selected materials, the extent and depth of the repaired area, the sub- base and ground conditions will fix the problem.
Mike Sondalini – Maintenance Engineer
DISCLAIMER: Because the authors, publisher, and resellers do not know the context in which the information presented in the articles is to be used, they accept no responsibility for the consequences of using the information.
We (Accendo Reliability) published this article with the kind permission of Feed Forward Publishing, a subsidiary of BIN95.com
Web: trade-school.education
E-mail: info@trade-school.education
If you found this interesting you may like the ebook Pumping Basics.
I’ve always wondered why some roads had weight limits posted, and now it makes sense. I didn’t know that weight would cause so much wear and tear on a road. I like your tip to get an expert to assist you in determining the cause of failure before making repairs. Is it common to have to repair only the bitumen, or is it usually the sub-base needs repairs too?
Hi April, to answer your question it really depends on the nature of the damage. I could be slipping under the roadbed due to water or the vibration/compaction. I could be a breakdown of the roadbed, or it can be simply damage to the surface. They are all related in how they support vehicles and responds to the loads. A break or crack in the surface can lead to water damage to the lower layers leading to more damage to the surface.
I live in a small mountain community with private roads. In a short walk I can see a range of damage, some we should maintain other we have to repair the roadbed.
Cheers,
Fred
Good explanation of how roads are paved and how they are repaired. Thanks so much for sharing.
very welcome Drew, thanks for the comment and kind words. cheers, Fred