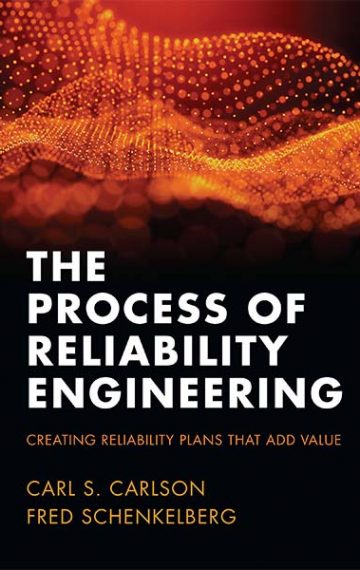
- Publisher: FMS Reliability Publishing
- Available in: Paperback
- ISBN: 978-1-938122-12-5
- Published: March 1, 2023
The Process of Reliability Engineering
The book is now available worldwide in paperback – ePub/Kindle version coming soon.
Please find the links to the appendices and more below.
Creating Reliability Plans That Add Value
“Every engineer and manager should own this book” ~ Bill Haughey, vice President, ReliaTrain
Achieving high reliability in products and processes is essential for reliability engineering and management. Regardless of your position in the organization, whether you are an engineer or a manager, you have a role to play in achieving high reliability. It is part of your job. Yet, little is written about this important objective.
There are plenty of books and resources on performing the wide variety of reliability methods and techniques. The methods of reliability engineering are well documented. What is missing is when and how to integrate the right set of methods into the product development process, putting it all together so that one is likely to obtain the desired results. The Process of Reliability Engineering is your roadmap to meeting reliability objectives.
No matter where you are on the supply chain, whether part of a Fortune 500 company or a startup, your customers want trouble-free products that work as promised.
Readers will learn:
- The difference between reliability engineering and reliability management and why it matters.
- The underlying philosophy for creating a reliable product.
- The six steps to achieving high reliability with any product or process.
- Why most reliability plans do not work as intended and how to learn from these lessons.
- What is a reliability strategic vision, and how is it created and used.
- What are the missing elements to achieving your organization’s reliability vision, and how to use them in creating a reliability plan.
- Why decisions matter and how to support critical reliability-related decisions.
- How to select the vital few reliability methods to close the gaps and support critical decisions.
- The correct procedure for writing and executing reliability tasks.
- Case studies, examples, and lessons learned, focusing on practical application.
- Timeless application tips that apply to any industry.
- Soft skills for building credibility and influence.
Whether your role is product or process engineering or management, we should aim to achieve the highest possible reliability and safety in our products. Join us on a journey to creating effective reliability plans that add value to your organization.
A great resource for those wanting their organization to implement or improve product reliability. It contains many hard earned nuggets of wisdom learned from years of practicing reliability embedment and execution in projects. ~ Daniel C. Conrad, Ph.D. Director Design Quality, Relaibility, and Testing
Excerpt from the book’s preface
When we began writing a book about reliability management, it dawned on us that there are plenty of books and resources on how to conduct failure mode and effects analysis (FMEA), accelerated life tests, and failure analysis and explaining the rest of the ways we work. The methods of reliability engineering are well documented. What is missing, in our opinion, is when and how to use those methods well. How do you put it all together in such a way that one is likely to obtain the desired results?
We both have long known that performing reliability activities, such as facilitating an FMEA or analyzing data from an accelerated life test, is just one element of managing reliability within an organization. The culture in an organization concerning reliability decision-making and how reliability is thought about and prioritized is more important than a well-fit Weibull curve. Part of managing reliability is managing the culture, which means focusing on how decisions are made. It means creating processes that enhance our ability to ensure that each decision includes the appropriate reliability information and priority.
Downloads, Supplements, and Appendices
Given that the details in the appendixes and references continue to evolve, plus the desire to shorten the overall length of the printed work, you may find the appendixes and references online with the links below.
Appendix A: List of Generic Questions to Consider When Conducting a Gap Assessment
The appendix lists potential questions to consider when performing a reliability gap assessment. This list is not meant to be a template and should only be used as thought-starters. The list of questions used in a gap assessment should be suitable for the circumstances and scope of the individual project.
Appendix B: Description of Decision Types
As an aid when selecting methods intended to inform key decisions, we have found that we generally face six different types of questions:
1. Prevention: What can we do now to avoid failures or improve reliability?
2. Comparison: Which design, vendor, or procedure option is better considering reliability?
3. Priority: Where should we focus our resources to best improve reliability?
4. Resources: Who and when should accomplish a specific task?
5. Objective: How do we set or identify the reliability and availability performance objectives, goals, or requirements?
6. Measurement: What is the reliability performance now or expected to be in the future?
Appendix C: Reliability Methods Sorted by Method Category
This appendix lists reliability methods sorted by category with decision type annotated. Keep in mind that this is not an exhaustive list of tools, techniques, or methods but a subset thereof that may be useful as you create a reliability plan. It is a list to provide awareness of common methods that aid in creating both a reliability plan and a highly reliable product.
Each listed method includes a very brief description of the method and the typical output. We have found many references for executing each method, yet few detail why one would use a method. Therefore, we mention what each method provides to assist in matching the best method for your plan’s needs.
PRE Reference List – expanded and with active links
An alphabetical listing of all cited references in the book, plus most have links to locate the source document. Our intention is to regularly update the list with additional information that we find useful for the range of topics in the book.