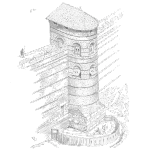
Chemical corrosion can destroy the containment materials in contact with a process.
Means exist to mitigate and even prevent chemical corrosion. This article focuses on several such methods.
Acceptable corrosion
At times chemical corrosion is acceptable and one need only allow for it by using thicker materials. An example is the storage of sulphuric acid in mild steel tanks at ambient conditions and concentrations higher than 80%. Though the acid attacks the metal, the rate of corrosion is extremely slow.
Using thick walled steel tanks with a corrosion allowance which takes decades to thin can be a cost-effective option. At 80% strength sulphuric acid will corrode a 12 mm thick wall tank to less than 6 mm in about 6 years.
Sulphuric acid absorbs moisture from the air. If the top layer in a mild steel tank is left undisturbed it will dilute and attack the steel. A 12 mm steel plate can corrode through in 12 months. Circulating the acid weekly, if it is stored in carbon steel tanks, will reduce this problem.
For small bulk quantities of sulphuric acid, a suitable plastic tank can solve the storage and corrosion problem cheaply.
Select chemical resistant materials
Using more resistant materials will reduce the effect of a chemical attack. Specialist metals and non-metals to contain aggressive environments are available. These can be expensive and their use is based on their cost effectiveness.
In particular, select low corrosion rate metals for flexible diaphragms used in process instrumentation.
It is false economy to select a 316 stainless steel diaphragm for a pressure transmitter on a tank of 98% sulphuric acid.
Though corrosion tables indicate 316 stainless has a low corrosion rate, experience shows that after two years of service the diaphragm can fail by pin holing. For an additional 20% cost, a Hastalloy C diaphragm provides a corrosion life 10 times longer.
Compatible coatings and linings
Prevent chemical attack by coating in a material unaffected by the chemical.
Rubber lining of hydrochloric acid storage tanks and plastic lining of process piping are examples. Teflon coating can protect a stainless steel sparge feeding sulphuric acid into a mixing vessel. Polyurethane liners can be sprayed onto tank walls.
Rubber linings normally fail at joins.
Check the correct procedure is used when they are mounted in place and test for holidays (pin holes) with spark testing.
Beware changed material properties
Heat from welding processes alters the metal properties at the heat- affected zone (HAZ) of the weld.
Stresses are introduced into the metal and grain microstructures are altered. Consideration of the welding method, weld procedure and use of stress relief can mitigate the effects.
The effect of welding is particularly evident when hot caustic solutions are contained in mild steel vessels. If carbon steel is used with hot caustic soda it is necessary to stress relieve the welds.
Unless stress is relieved, a chemical attack can occur at the HAZ of the welds where stresses are high.
Consider the changing process conditions
Using corrosion tables without considering all the process conditions can lead to poor materials selection.
Most published data on compatibility do not take into affect agitated conditions. Some data only applies to ambient temperatures. Data is normally not available on the effect of aeration. Nor is data readily available on the effect of other contaminants, for example, chlorides with stainless steels.
In uncertain or changeable situations will occur in a vessel consult the material manufacturer and ask for their advice. If they cannot help, then the only remaining option is to conduct your own laboratory tests or field trials.
The chemical compatibility table below was derived from numerous published data. The most conservative temperatures were selected. Where no temperatures are shown ambient conditions apply.
Chemical corrosion control and mitigation require creative use of a few basic principles.
Please login with your site registration to view and download the Process Chemicals Corrosion Compatibility Table.
If you haven’t registered, it’s free and takes only a moment.
Mike Sondalini – Maintenance Engineer
DISCLAIMER: Because the authors, publisher, and resellers do not know the context in which the information presented in the articles is to be used, they accept no responsibility for the consequences of using the information.
We (Accendo Reliability) published this article with the kind permission of Feed Forward Publishing, a subsidiary of BIN95.com
Web: trade-school.education
E-mail: info@trade-school.education
If you found this interesting you may like the ebook Process Control Essentials.
Leave a Reply