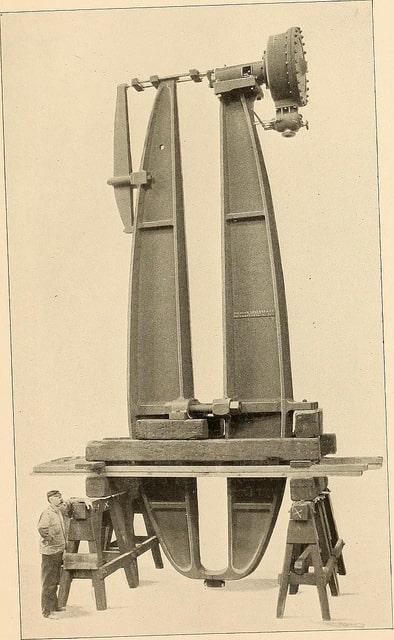
The Business Skills of a Good Reliability Engineer
Knowing how estimate sample size or create a Weibull plot is not enough today.
Just having technical skills, while essential, is not sufficient.
Having a master of business administration (MBA) may be helpful it is not required, yet knowing the warranty and brand cost per failure is essential.
You also need to know which analysis to conduct and how it fits into the larger program, organization, and how it impacts your customers. You need to know the business side of your work as well.
You need to understand the business connection as you create plans and finalize analysis. Each test proposed should include a business connection. Each improvement proposed has to balance with the other priorities and objectives and remain compelling.
What is Important to Your Organization?
I don’t know as I write this what is important to your organization today. It varies, even within an organization and over time. You do need to know what is important and why to become a good reliability engineer.
It is not enough to do what someone tells you to do. At first that may get you starting yet how you connect your work to adding value become essential. Practice finding the connection with every task.
Ask questions.
- When do you need this information?
- When will this need an initial review?
- When do you need a budget estimate?
- Who will review this report?
- Who will need this information?
- What level of reliability knowledge does the audience have?
- What level of detail is necessary?
And, so on…
The idea is to find who needs what by when and why?
This helps you plan, focus and deliver what is considered important at the moment in your organization.
Typical Priorities
For a high volume consumer product sold during the holiday period, time to market may be the top priority. This is because a delay to shipping means the loss of sales for the year. Missing the deadline is not an option. Thus, your work as a reliability engineer has to focus on how you can minimize the risk to any delays.
Now, you know that finding a critical reliability issue late in the process may delay the program, therefore focusing on reducing the chance of a late discovery is your focus. Early testing and development work on the highest risk element may help you identify reliability risks that have a long lead time to test and evaluate.
For a industrial product with relatively low volume the time to market pressure is not as intense. In this case, the brand image may be paramount. Thus getting the initial units as reliability as customer expect becomes an overriding priority.
One of the issues with this situation is the lack of prototype systems to evaluate. You may not have the capability to test full systems in any quantity prior to to the start of production, if ever. Thus, you work to identify and characterize each potential failure mechanisms becomes critical. The ability to create a viable system model allows you to prioritize your work on improving the critical few elements that will impact system reliability performance.
Other priorities may focus on cost reduction, cutting edge feature sets, or ease of use. Your organization likely has a clear priority. It’s then up to you to connect your work in reliability engineering to that priority.
Now Connect Each Reliability Task to the Value it Provides
For each reliability task proposed or delivered what is the value it provides connected to the primary priority (or secondary priority) in a clear and concise way. If the task or activity doesn’t add value, why are you doing it?
In the high volume consumer product situation, reducing the risk of a shipment delay provide value. Let’s say you are proposing HALT early in the program. How would that add value? By potentially identifying design or manufacturing faults if discovered late in the program would delay the project, then you arguably reduce the risk of delays by some amount.
For the low volume complex equipment situation, a HALT would improve the ability of the team to find and solve complex issues that may otherwise go undetected. Again, HALT would add value. In each case there is not a hard and fast formula yet there is a clear step by step connection between the task and the value to the organization.
Summary
There are two steps here. One understand the business and customers to the extent that you clearly understand what is important. Second, articulate the value related to the business priorities for each reliability task or activity.
To see more examples and ways to show value, see the book Finding Value: How to Determine the Value of Reliability Engineering Activities.
Your skill at connecting your work to value enhances your ability to focus on what is important and necessary. Thus it helps your customers, organization and your career.
2016.03.26
Thanks. Fred!
This article is encouraging me, because I’ve been trying to connect quality/reliability improvement activity with a business such as value.
But I could not know what activities is connected with values directly or indirectly.
Fred, do you have some experience or some best practices?
Could you give me the advice?
Hi Daniel,
Thanks for the note and yes connecting your reliability activities to value is essential. You can find more about this topic along with a number of examples in my ebook, Finding Value
http://lucas-accendo-site-speed.sprod01.rmkr.net/finding-value/
it’s free to download with sign up with the site, or you can buy a hardcopy, if you’d like.
Cheers,
Fred
Thank you for the advice, Fred. I make sure that it could be helpful for me.
Hi Daniel,
You are very welcome and please do enjoy and create value with each of your reliability activities – Cheers,
Fred