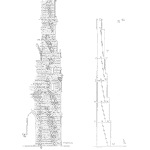
What is added to the capital investment?
Your upfront capital investment must go beyond engineering, procurement and building costs. Additional activities that will need to be done that fit within the 2 – 3 % of capital cost figure are:
RCM analysis on the new design (preferably at both concept and detailed design phases so you can incorporate design change recommendations easily)
- Consolidating RCM analysis outputs into jobs, task lists, operator inspection routes, etc.
Writing procedures and practice descriptions to go with the operator tasks.
Planning for future maintenance work (complete job plans including other logistical support needs such as lifting apparatus, tools, test equipment, spare parts, etc.).
- Putting the defined and planned jobs into your work order management system, setting it up with its library of standard jobs.
- Setting up the proactive maintenance program schedules based on defined task frequencies.
Skills definition – complete descriptions of skills required to do all the work that is forecast
Training needs analysis – defining the gaps that will require additional training for existing staff and for induction of new staff.
- Determine how to deliver the needed training.
- Definition of training facilities requirements.
Defining the spares requirements (analysis of spares and their demand frequencies to determine what to stock, how much and where).
- Repairable item analysis (to determine what to spare in support of repairables).
Defining tooling, shop and other support equipment requirements
- Determination of what to outsource or keep in-house
Documentation definition together with a “management of change” process to keep it up to date.
- Determine asset hierarchy
- Define all technical documents that are required
- Catalogue and store documentation that you acquire with the asset
Over and beyond that 2 – 3 % spend you will also need to invest in things you should be buying anyway, but now you’ll be buying what you need, exactly what you need, where you need it, in the right quantity, and in sufficient time to serve operational needs. If this amounts to more than you may have expected to spend, it’s because your previous spending estimates were understated and would have left you wanting once you enter service with your new capital asset.
These additional items include:
- Spares, tools, test equipment, shop equipment, calibration equipment
- Facility modifications / build for training, shops, laydown areas, store rooms
- Support IT (CMMS, EAM, spares management, etc.) if not already in existence and use
- Staffing – hiring of new human resources
- Training (courses, materials, delivery)
- Contracting set up – for outsourced services such as repairs that are not done by in-house personnel, outside repairs to repairable items, specialized analysis services such as lube, vibration, infra-red, ultrasonic, etc.
- Documentation that does not come with the capital assets:
- Training syllabi, system diagrams, new procedures and practices, process diagrams and definition, etc.
Conclusion
All of this may seem like a lot to an organization that has not done this well in the past. It may even seem like overkill to some, but consider what will be missing if you don’t do it. Consider the disruption, loss of production, the risks to safety and the environment that could arise if you are not prepared properly. Consider the time it will take to ramp up to full capacity if you are stumbling through teething problems and their solutions as you gradually come up. Consider the loss of production / capacity that accompanies that long ramp up period.
Can you afford “failing to plan” or can you now afford to “plan for success”?
Leave a Reply