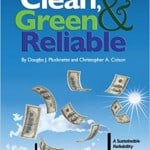
Clean, Green & Reliable – Improving Equipment Reliability and Reducing Energy in Manufacturing Facilities
I first became interested in manufacturing reliability nearly twenty years ago working as a maintenance mechanic who had a personal interest in improving the reliability of individual assets by searching through our maintenance history for areas where we were spending the most time and money in regard to emergency/demand work orders. Using the history we had in our database we used the 80/20 approach to identify the 20% of our assets where we spent nearly 80% of our maintenance budget. Once we identified a system or asset to work on we would use a cause-map or root cause analysis to identify the potential causes of our equipment failures, understanding these causes we would then look to identify potential redesigns to eliminate or reduce the frequency of equipment failures.
Understanding Cause and Effect Well
While working on these problems and identifying solutions as a group we also began to understand the power behind the relationship between cause and effect noting that a single cause could have several effects and any given effect could also have several causes. We also noticed in finding solutions to causes of many equipment failures, the impact these solutions reached far beyond the measures of equipment reliability.
While the benefits of equipment reliability are most noted for reducing the cost of maintenance, the benefits of reliable assets reach far beyond the cost of eliminating emergency and demand maintenance. In wrapping up each project we highlighted the benefits and savings derived to drive home the point that equipment reliability would deliver more than a reduction in maintenance costs. For each project we would report the following information.
- Overall Equipment Effectiveness (OEE) in the months before the project and following implementation.
- Number of maintenance man-hours dedicated to maintaining the asset 12 months prior to the start of the project and again in the months following implementation.
- Parts costs before and after the project
- Energy usage/costs in the 12 months prior to the start of the project and usage in the months following implementation.
Nearly every time our teams reported this information in meetings to management I found it interesting that someone would comment that the savings and increase in productivity were significant but the energy savings were insignificant. “As a company we generate our own utilities so the 25% reduction in energy usage for this asset will not result in a cost savings to the company, unless the savings were significant enough to warrant the shut down or one of our boilers or turbines it has no impact on the company bottom line.”
“Thanks for the effort but next time leave the energy piece out of the equation!”
Today Energy is Important
Fast-Forward twenty years and things are a little different, most of the MBA’s I used to work for had to go find employment someplace else. It would seem that for most all they learned in graduate school was to nod their head yes after our former CEO demanded they do something stupid.
Welcome to the Simon school of business. Simon says nod your head yes!
I believe you would now get a totally different response should they be able to reduce energy consumption at any manufacturing facility. Regardless of ones beliefs in regard to global warming, reducing energy consumption it the right thing to do especially when we can show that this reduction in energy consumption is a byproduct of improved equipment/manufacturing reliability.
As a reliability engineer and consultant, I find it exciting that nearly every major company in the world includes pages in regard energy efficiency and environmental responsibility on their corporate web sites. I’m excited because I know that reliable systems, reliable processes, and reliable assets are both energy efficient and environmentally responsible.
A Book Idea Comes About
The idea to write this book came out of some discussions I had with Terry O’Hanlon in regard to my purchase of the domain name Reliabilityisgreen.com an idea I had while writing the RCM Blitz book. Terry and I have both experienced how improved reliability can have a positive impact on energy efficiency and it was Terry who had the idea for this book. While we both have experienced this relationship between manufacturing reliability and energy efficiency the true experts who can answer the questions of what we need to do, why it works, and the results we should expect will be key contributors to this text. With this information and a few real life case studies on how equipment reliability improved energy efficiency we hope to enlighten the masses on how reliability delivers energy efficiency.
As the project moved forward and Chris Colson came on board, Chris and I started researching and reading about the various reliability tools and methods that made general claims regarding energy savings. While some of these claims have been substantiated, there are others where the book is still out. The most popular claim in regard to energy saving is up to 20%. If you read that some device can deliver up to a 20% reduction in energy costs or a 20% improvement in energy efficiency, use a bit of common sense and ask for a case study or client testimonial. If there is one thing I know about Manufacturing Managers, they will not release fudged numbers to the public.
Chris and I also wanted this book to be different than the other books aimed at business in regard to energy savings. I bet I can find at least 20 books that talk about reducing energy usage by doing a upgrade to the building lighting, windows and office thermostats. With plenty of this information available, we wanted to write about some common systems and technologies where if they focused some time and effort, they would see a quick return on investment and a improvement in reliability.
While this effort has taken nearly two years to complete, we are pleased with the results and believe you will be as well.
Leave a Reply