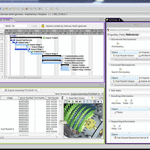
The Advantages to a Properly Configured and Implemented CMMS can be Numerous.
Managing all the information and data in maintenance can be overwhelming, yet it is critical to the success of your organization. If you are not yet using a CMMS, or thinking of changing it, you could be in for some major improvements.
A recent study by Software Advice concluded that a cloud based CMMS can offer three main benefits to organizations. These benefits are the type of benefits that will make a difference in your organization and deliver bottom line results. These three benefits are:
Proper Prioritization of Maintenance Work
The study indicates that a CMMS can easily improve the business process involving all aspects of the work order system. When the work order system is in the CMMS, it can coordinate and ensure that all other aspects of maintenance are connected. This includes the storeroom, documents, and performance management systems.
The study noted that, “Arguably the most impactful benefit of maintenance software is the ability to strategically schedule and prioritize work orders. This allows users to devote precious labor hours to the kinds of tasks that keep the organization running and profitable, while eliminating or de-prioritizing work that has less of an effect on the bottom-line.”
The benefits to a good work order system manifest itself through improved wrench time, which reduces overtime and planned downtime.
Just In Time (JIT) Maintenance thru CBM
Over maintaining can be just as detrimental as under maintaining, resulting in poor equipment reliability. Newer CMMS’ address this through the integration of the PdM data enabling Condition Based Maintenance.
When using a modern CMMS, “Condition-based maintenance gives maintenance managers actual condition data to work with, meaning they can reduce labor by only scheduling work on an asset when the data indicates that a problem is developing.”
This facilitates effective maintenance as the team is only working on what needs to be worked on. This increases uptime and reduces costs.
Reporting and Analytics
Without data, we are at best just guessing what we should do. Would you like your financial advisor guess? The answer is probably no, so why should you as a maintenance professional do the same thing? Proper data allows for reporting and analytics which allow you to make the right decision for the business and support those decisions.
A modern CMMS “With reporting features, users can identify trends in asset data to determine which assets may need more attention. It may also show that a certain machine doesn’t need quite as many checkups throughout the year, freeing workers to focus on more critical assets.”
This once again allows for effective maintenance while driving down costs. This is most prevalent in CAPEX, where assets are replaced based on data, not intuition.
Quantify the Savings of a CMMS
But how do you quantify the savings of implementing a CMMS? First you need to know your cost of downtime, which can be calculated below using a calculator developed by Software Advice:
Once you know the cost of downtime, you need to determine how much you can save.
Based on studies of properly implemented CMMS, and I use the term properly loosely, as typically most organizations do not implement a CMMS with all the required data and configuration. The end results is a CMMS that is only 50% used. When successfully implemented and more than 50% of the functionality is used, you can typically expect improvements in the maintenance of;
- 5-10% reduce of unplanned breakdowns based on a systematic failure analysis. (this aligns with the 3rd finding of the study)
- 5-10% increase in productivity gains, increased safety. (this is partially align with the first finding)
- 3-5% improvement in backlog and outage management (this is aligned with the first finding)
- 3-5% improvement in material management (less stock outs, less rush orders, ability to find the parts, less over stock)
- 3-5% reduction in PM workload as the right PMs are being done, (aligns with the 3rd finding)
Based on these numbers and the cost of your downtime, you can calculate the approximate value of the improvements if you fully implement a CMMS successfully.
It is important to remember that the CMMS is only a tool and requires the right information and analysis to make the results a reality. The team must be staffed accordingly and people held accountable. In addition you must have a CMMS fit for purpose.
How do you select a CMMS? That will be the topic of the next blog post.
Remember, to find success, you must first solve the problem, then achieve the implementation of the solution, and finally sustain winning results.
I’m James Kovacevic
HP RELIABILITY
Solve, Achieve, Sustain
Follow @HPReliability
References:
How 3 Modern CMMS Tools Increase Machine Uptime by Taylor Short of Software Advice
CMMS Cost Justification: How Do You Justify the Purchase of a New CMMS System? by John Reeves
No Fields Found.
Thank you for sharing those advantage of cmms software in the organization. My friends and I decided to have CMMS to make the organization report make easier to generate.
Great piece that highlights the benefits of a CMMS