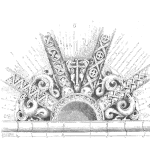
A confined space is anywhere not normally meant for human habitation in which access maybe restricted and the conditions in the confinement may be inadequate to support life or could cause engulfment. Obvious places are tanks, vessels, silos and below ground pits. The less obvious ones are cold rooms, areas of plant sandwiched between machinery and equipment, tip truck trays and open pit mines.
Keywords: risk assessment, hazard identification, job safety analysis, safe atmosphere.
WHAT IS A CONFINED SPACE?
A confined space is anywhere not normally meant for human habitation in which access maybe restricted and the conditions in the confinement may be inadequate to support life or could cause engulfment. Obvious places are tanks, vessels, silos and below ground pits. The less obvious ones are cold rooms, areas of plant sandwiched between machinery and equipment, tip truck trays and open pit mines.
In Australia it is law that entry into confined spaces must meet the requirements of Australian Standard AS 2865 – 1995 ‘Safe working in a confined space.’
REQUIREMENTS FOR CONFINED SPACE ENTRY
Listed below are the key issues when conducting work in confined spaces but AS 2865 is the overriding requirement.
1. Request for work.
A request for work in a confined space must be documented and authorised by the ‘owner’ of the confined space.
2. Can work be done without entering confined space?
Can be done from outside the confined space? Consider modifications to remove the need to enter the confined space or to make exit and entry easier and safer.
3. Hazard Identification/Risk assessment.
Before entering a confined space a documented hazard identification and risk assessment must be done by competent persons with employee involvement. A register of confined spaces on-site must be kept and be up-to-date.
All risks identified in the risk assessment are to be eliminated or reduced to acceptable levels by appropriate methods prior to entry into the confined space.
4. Isolate parts, materials and services.
Prior to entering a confined space all potentially hazardous services, including all process services, normally connected to the space are isolated to prevent:
- introduction of any materials, contaminants, agents or conditions harmful to persons occupying the confined space;
- the activation or energising in any way of equipment or services which may pose a risk to health or safety of persons
5. Cleaning and purging (if necessary)
Where appropriate the confined space is to be cleared of contaminants by use of a suitable purging agent. Gas mixtures with oxygen at greater than 21% by volume are not to be used for purging or ventilation.
6. Evaluate atmosphere
Before entering the confined space it must
- contain a safe oxygen level;
- have atmospheric contaminants reduced to below the
relevant MSDS exposure limits; - be free from extremes of temperature;
- ensure the concentration of flammable contaminants in the atmosphere are below 5% of the LEL (Lower explosive limit on the Material Safety Data Sheet).
7. Is atmosphere safe for entry? Eg safe oxygen level, no toxic gases.
No entry or work is allowed in the confined space or on the outside of the confined space if:there is
- there is risk to health or safety of persons in the confined space or working upon its surface; a risk of fire or explosion exists.
- a risk of fire or explosion exists.
8. Ventilate (to maintain environment)
Ventilate the confined space by natural, forced or mechanical means. If mechanical means are used insure their use does not introduced unforeseen hazards and risks (Eg. diesel fumes, additional power cables, etc).
9. Issue personal protective clothing and safety equipment (PPE)
Where a safe oxygen level cannot be achieved or the atmospheric contaminants cannot be reduced to safe levels no person enters the confined space unless equipped with suitable PPE including air supplied breathing equipment.
Equipment required to safely enter the confined space is to be appropriate for the confined space and be maintained in proper working order. All PPE and rescue equipment is to be fitted to suit the individual.
10. Authority to enter or work in confined space
Subject to the completion of a proper risk assessment, written approval in the form of an entry permit must be provided prior to entry.
No one can enter a confined space without a permit that:
- includes any precautions or instructions necessary for safe entry and work execution;
- is provided to the person in direct control of the work in the confined space;
- records which persons enter the confined space
- provides proof the persons involved in the work are advised of, understand and comply with the contents of the entry permit. Appropriate rescue and first aid procedures and provisions are to be planned, established and rehearsed.
11. Entry to confined space
Prior to any person entering a confined space, and during occupancy of the confined space, appropriate signs and protective barriers are erected to prevent entry of persons not involved in the work.
Where a risk to health and safety is identified in the risk assessment, no person may enter a confined space unless a stand-by person(s) is present outside the confined space.
Suitable equipment identified during the hazard and risk assessment is to be provided, where necessary, for:
- personal protection;
- rescue;
- first aid;
- fire suppression.
Training is required for all persons working in or on the confined space and in all relevant activities related to entering and working in or on confined spaces.
The training shall cover at least the following: the hazards of confined spaces;
- hazard assessment procedures;
- hazard control measures;
- emergency procedures;
- the selection, use, fit and maintenance of safety equipment.
Training is to be provided to all persons who:
- perform work in or on confined spaces;
- perform confined space assessments;
- issue entry permits;
- design and layout confined spaces;
- manage and/or supervise persons (employees and contractors) working in or near confined spaces;
- maintain equipment used for/during entry;
- purchase, distribute, fit, wear and maintain personal protective equipment;
- are on stand-by;
- are involved in rescue and first aid procedures.
12. Test/monitor atmosphere regularly
Where the hazard and risk assessment indicates a potential for the atmosphere within a confined space to change due to release or by introduction of contaminants, arrangements are to be made to continuously monitor, or at appropriate intervals, retest the atmosphere within.
An atmospheric condition test is to be conducted at the start of each shift prior to entry into the confined space.
13. Approve for return to service
Confirm and acknowledge in writing that work in the confined space has been completed and that all persons involved in the work have left the space before giving authorisation to return the confined space to service.
Mike Sondalini – Maintenance Engineer
We (Accendo Reliability) published this article with the kind permission of Feed Forward Publishing, a subsidiary of BIN95.com
Web: trade-school.education
E-mail: info@trade-school.education
Leave a Reply