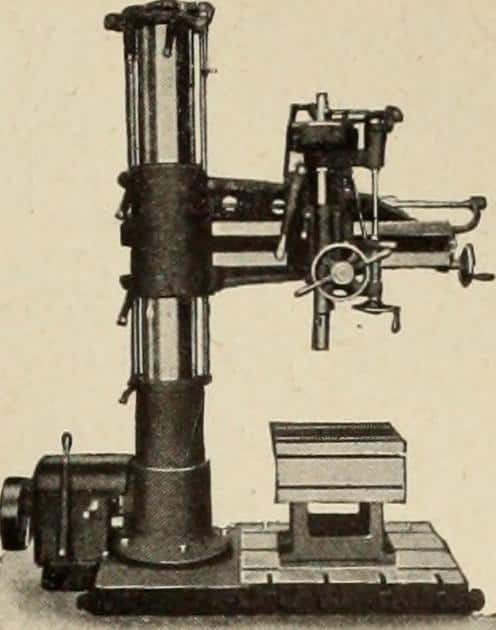
WIIFT and Reliability Measures
WIIFT is “what’s in it for them”. Similar to what’s in it for me, yet the focus is your consideration of what value are you providing your audience.
As a reliability engineer you collection, analyze and report reliability measures. You report reliability estimates or results. Do you know how your audience is going to use this information?
Consider WIIFT when reporting reliability.
There are many reasons people look at reliability measures. Let’s explore a few WIIFT situations and build your ability to consider WIIFT when preparing and reporting reliability values. Keep in mind that underlying any metric is decisions.
Field Failure Rate Data
When monitoring field data failure rates, the leadership team may consider the allocation of additional resources to improve future field reliability performance. Or the data may suggest a product recall. We monitor to identify actionable situations. We want to reinforce good performance and thwart the impact of poor performance.
What is in it for the person monitoring the failure rate data? Spotting a trend and taking prompt action may save a product line significant revenue. The appropriate resources are assigned to work on product improvement, while other resources focus on other priorities. When the reported failure rate data and the decision making work well, problems are spotted and resolved before the issues become major problems.
The trick is having clear, concise and complete data that allows the identification is trends or abrupt changes in the failure rate. Averaging and reporting MTBF or MTTF tends to obscure this information. The use of Weibull cumulative distribution plots with expected performance indicators may provide sufficient sensitivity for the monitoring task. Help your decision makers make the right decisions.
Effectiveness of Maintenance Program
One way to determine if a maintenance program is working well is to track availability. A possible key performance indicator is the number of unplanned maintenance actions per month. Simply reporting availability may work, yet it is just an average for a time period and lacks clear trending information.
Rather than create a plot of week to week MTBF or Availability values, consider using a mean cumulative function plot. The non-parametric view of the cumulative number of repairs over time immediately makes clear trends related to the equipment and its care.
A plot that bends upward suggests each repair leaves the equipment in a little worse shape, whereas a flattening out bend suggest the equipment is running longer between maintenance actions. See the article by Wayne Nelson for more information on this visual technique to help our team understand and make better decisions concerning equipment maintenance.
The WIIFT may concern planning, warehouse costs, and maintenance budgets. Making decisions to keep great maintenance practices versus move to a reaction to failure stance relies on having a grasp of the trends. Help decision makers get the best running equipment that permits consistency and predictability of equipment throughput.
Comparing Component Reliability from Two Vendors
Let’s say we have two hard drive models in our possible solution. Which is a better drive, reliability speaking? We can compare data sheets, compare the reported MTBF values, or we can provide a bit more clarity.
This may take some work to either gather or create (testing) the time to failure data. How long and under what conditions did the drives operate before failure. Even better is you also know how many drives did not failure over what period. Plus, having detailed failure analysis of each failure would help, too.
In short, let’s assume the drives failure for a dominant failure mechanisms related to how your product and customers will use the drives. A Weibull (or appropriate distribution or non-parametric) plot of time to failure data allows your team to visualize the data and the trends over time. Placing both sets of data on the same plot enables the comparisons required to make a good decisions.
Condensing the data to a single value, like MTBF, hides essential information. Knowing if the failures occur mostly in the first month or last month has major impact of vendor selection. Knowing the expected failure rate over time enables the team to consider sparing, cooling, redesign, and other factors that may minimize the eventual failure rate. Selection based on a single and often value MTBF value for each drive is fraught with ambiguity.
The WIIFT is making the right choice. If the decision makes care about meeting business objective and keeping customer happy, then selecting the right vendor is key.
Summary
In each case get time to failure data and do not use a grand average value, like MTBF. Plot the data. Parametric or non-parametric, plot the data to “see” what is going on. Help you decision makes make the right decisions with clear, concise and complete information. Help them get WIIFT.
Yes, Years ago I helped build a FRACAS system and used a Cusum function to show rate of change of failure events – The inflexions in the trends are so much more informative.
Fitting these trends on log-log graphs help us choose distributions.
thanks Charles – very true it is the bumps, rises, spikes, etc that matter the most.
Also, btw, sorry the note is late this week, the scheduled post didn’t post…
hope to get back on schedule next week.
Cheers,
Fred