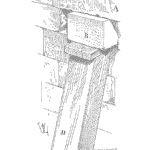
What you will learn from this article.
- Control loops automatically correct unwanted changes in a process.
- A control loop consists of components to detect and adjust the process.
- Control loop complexity reflects the accuracy and speed of control.
- Explanation of ‘open loop’, ‘closed loop’, ‘feed back’, ‘feed forward’.
The sole purpose of using process control in, say, the making of beer, is to detect what is happening during manufacture and to decide if something needs to be changed to insure the beer meets the necessary specification. The key words are ‘to detect’, ‘to decide’, ‘to change’ and ‘to meet specification’. A control loop can do all these things automatically.
Control Loop Components
A control loop is made up of the components shown in Figure No 1. It consists of:
- a sensor to detect the process,
- a transmitter to make the sensor signal into an electrical signal,
- a controller that tests that the signal meets a pre-set value and
if not makes the adjustments required, - a final controlling element(s) that physically move and alter its
position (e.g. a control valve), - a converter that changes an electrical signal into a proportional
force or a force into an electrical signal (a transducer), - the medium (like steam, chilled water, etc) that provides the
energy change to the process to produce the correction.
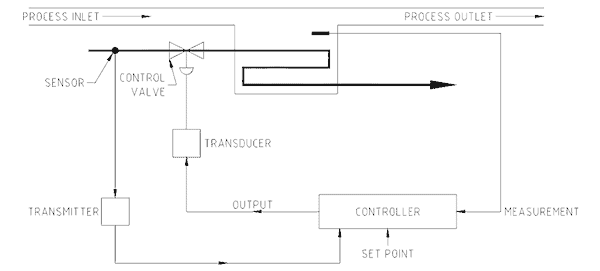
Control Loop Complexity
Control loop complexity depends on the final product specification. If the product acceptance range is wide then simple, inexpensive control loop components can be used. However if the required final product specification is demanding, the control loop becomes more complex and expensive. This is necessary in order to react fast enough to changing process inputs in-time to still produce the output product to specification.
Open and Closed Loops
Very simple control loops that detect an incoming process variable and display the value to an operator are called ‘open loop’ control systems. In this case it is up to the operator to make any changes to the process. As soon as a final control element is added to allow incoming process variable adjustment the complexity and cost of the loop rises sharply. The final control element requires a decision-making device (the controller) to signal it to move. Such an arrangement is called a ‘closed loop’ control system because the sensor’s signal controls the reaction of the loop from the initially detected process change right through to the finally detected adjustment. The entire change starts and ends (closes) with the sensor detecting the proper required conditions.
Feed Back — Feed Forward Systems
The requirements for the speed and accuracy of the control loop response determine whether ‘feed back’ or ‘feed forward’ control is used. Feed back control measures the final product and checks it is produced to within the specification tolerance. If it is not it within tolerance the final control element is adjusted to make corrections.
Feed forward control measures the incoming variables before they go through the process, making sure they are within preset tolerance before combining together to make the product. Feed forward control is the more complex and expensive method to use.
One can see that it is best to use the least complex and inexpensive control loop phylosophy possible. Complex loops require expensive components; great amounts of effort programming and tuning the controller; are easily ‘confused’ by abnormal process occurrences; require unending maintenance to retain their sensitivity; demand high levels of emergency spare parts and the presence of highly skilled operators and maintainers.
The right control loop choice can only be made when the product specification tolerance is well understood. If low cost control is required the product specification must have a wide range of customer acceptability. Tight tolerances add great cost.
Mike Sondalini – Equipment Longevity Engineer
Reference: Operative Certificate in Chemical Plant Skills Manual, Holmesglen College of TAFE, 1993
We (Accendo Reliability) published this article with the kind permission of Feed Forward Publishing, a subsidiary of BIN95.com
Web: trade-school.education
E-mail: info@trade-school.education
If you found this interesting you may like the ebook Process Control Essentials.
Leave a Reply