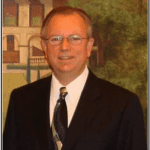
Guest Post by David Patrishkoff (first posted on CERM ® RISK INSIGHTS – reposted here with permission)
We are living in a time of great disruption and uncertainty.
Every organization is facing great risks. Some of these risks are visible and many others are hidden.
So, it’s crucial that every company develops and implements tools to identify, mitigate and transform risks into dramatic improvements and even disruptive innovations.
We believe that gamified risk management can strengthen and correct failing corporate initiatives and complement lean and six sigma tools to produce superior results.
Gamified risk management addresses leadership and cultural barriers that can undermine the path to greater performance.
This is our story:
Conducting a root cause analysis of their root cause analysis process
In an effort to significantly improve top and bottom line performance, a Fortune 50 high-tech company launched a global Lean Six Sigma (LSS) initiative.
It trained and certified hundreds of its employees to lead improvement projects in manufacturing, design, and administration. Several years into the program, management realized that many problems that appeared to be resolved by their LSS problem solvers, and were returning within 3-4 months.
This was a troubling situation.
As an outsider and Lean Six Sigma Master Black Belt and Risk Management Expert, I brought in to analyze why this strategic program was not working effectively.
I was given access to leadership, management, LSS staff and employees to conduct confidential interviews and group discussions. So, what were the challenges with lean and six sigma deployment?
Assessing cultural health with organizational cascades
An organization is a cascading system that originates with leadership and emanates throughout the work culture into work processes.
These cascades create good or bad performance and deliver feedback to leadership (Figure 1). If these feedback loops are working correctly, they are self-policing and self-regulating.
They encourage learning, innovation, and high performance. Without them, an organization will stagnate, struggle and self-destruct over time.
In a healthy organization, leaders do not assign blame for problems. They identify and address defective processes. If you engage good people in a flawed process, the flawed process will always win.
Figure 2 below shows the full list of 56 different internal risks that are present at each level of an organizational cascade.
Creating a cascading risk map of the organization
The analysis determined that 25, out of a possible 56, cascading risks adversely impacted the LSS Program (Figure 3).
These 25 major barriers included various leadership issues, cultural weaknesses, process inefficiencies, poor performances, weak responses to process and customer warning signs and absent learning loops.
These barriers to success were widely spread throughout the organization. Individually, these obstacles were annoying.
Collectively, they created a dominant cascading force that paralyzed the effectiveness of the LSS Program.
Self-destructive leadership activities
At the top of the cascade, seven major flaws in leadership attributes and practices disabled problem-solving efforts.
They included blame gaming, reckless spending on projects and programs, non-motivational, non-compromising, risky business expansion and false optimism (Figure 4). Process improvement leaders were blamed when problems returned, even though most could be attributed to management practices.
The organization was more focused on expanding the business through acquisitions than creating a high-performance work culture.
Many leaders supported a random whack-a-mole style of problem-solving.
Leadership embraced proposed solutions
When the Organizational Cascading Analysis was shared with top leadership, they accepted management responsibility for the cascading internal risks that blocked the performance of their LSS program.
They agreed to train all managers on the pivotal role they play in driving a high-performance work culture, process excellence, and employee empowerment during problem-solving efforts.
Within several months, the LSS Program was meeting their high expectations.
Stay tuned. In the following articles, we’ll describe how you can seamlessly integrate gamified Risk Management and Cascade Effect Thinking into your six sigma and lean initiatives.
Bio:
David Patrishkoff is President of E3 – Extreme Enterprise Efficiency® and the Founder of The Institute for Cascade Effect Research®. He is a Lean Six Sigma Master Black Belt, Adjunct Professor for Kettering University Master’s Degree Programs and the inventor of a Cascading Risk Management Methodology.
Prior to starting his consultancy in 2001, David held many worldwide senior executive positions in the automotive and trucking industry. Author email: david.patrishkoff@cascadeeffects.com.
Additional information can be found at:
http://www.cascadeeffects.com/home-1.html
http://leansixsigmaandbeyond.com/
Leave a Reply