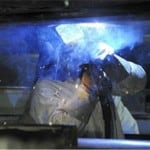
If you can’t sell all you can produce, then reducing costs is often the only way to improve margins, but that simplistic accounting perspective is not always the case.
Cost control is often thought to be key to attaining profitability but it the case of maintenance it can get you into trouble.
Cost control can have a big opportunity cost if you don’t take advantage of the opportunities you have.
Figure 1 shows the basics – as production increases, revenues, and costs both increase. Revenue is zero at zero production and increases to 100% at 100% output (if you can achieve it).
Fixed costs (e.g.: depreciation lease payments, energy to heat offices, someone to answer the phone, etc.) keeps the start point for the cost curve above zero.
In Figure 1 we show costs increasing as production output increases. At some point revenues eclipse costs and you are making money.
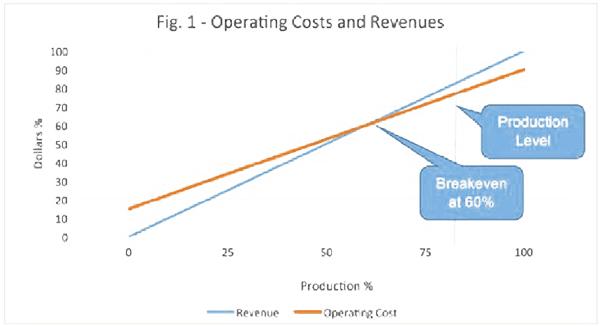
Production levels must be kept above the 60% breakeven point in order to generate a margin (earnings before taxes).
Margin is represented by the gap between the revenue and cost lines to the right of the breakeven point. Here we show production level at 80% of full capacity. At that level of capacity, the margin as shown is 5% of revenues.
Businesses are there to maximize earnings.
They can produce more, increasing revenues (assuming the market will absorb your production) and they can reduce costs. Cost reduction moves the cost curve down (vertically) if you can reduce fixed costs.
Cost reduction also reduces the slope of the line if variable costs are reduced. In the example here, I show a “worst case” scenario where fixed costs don’t change. We only reduce the slope of the cost line by lowering operating costs.
Any cost reduction (fixed or variable) moves the breakeven point to the left and increases margins. The gap between revenue and cost lines gets larger. That improved cost line is shown in Figure 2 with a new breakeven point at 50% of production capacity.
In this lower cost scenario, the operation produces a profit margin at lower production levels and the size of the gap between revenue and costs increases.
Even if production levels remain unchanged at 80%, the margin increases from 5% to 9% – a substantial improvement in profitability.
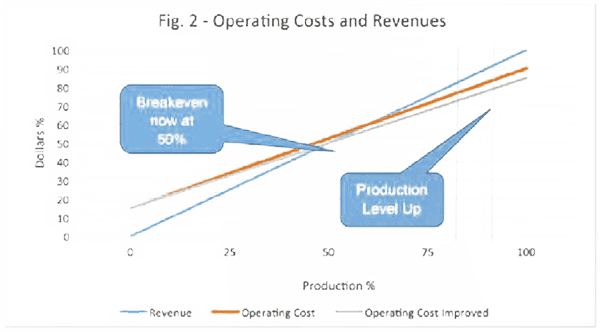
Let’s say we can use increased production to either sell more product in a healthy market or to reduce the number of shifts needed to meet the diminished demands of a tight market.
What sort of maintenance improvements will help us? Top level performers in maintenance often achieve 90% availabilities compared with an average of 80%.
Assuming we can utilize that capacity, then if we increase production levels from 80% to 90%, our margin increases to 12%!
What can we do to achieve that?
We need a more reliable plant to pull that one off because cost reductions alone won’t deliver more output capacity.
Let’s assume that our maintenance performance has been more or less “average”. In that case, our availabilities will be around 80%.
If our production staff can utilize full availability, then our maximum output will be 80% of full capacity as shown in Fig. 1. Maintenance costs vary from 5% to 50% of operating costs depending on your industry with an average around 20%. For illustration, let’s assume they are at 20%.
If we increase our maintenance performance to levels achieved in benchmark studies by high performers then we can reduce that cost by about 25%, taking it down to 15% of operating costs.
Our “improved” line on the graph illustrates that reduction at full capacity.
What sort of benchmark performance do high performers achieve?
Labor utilization (wrench time) increases through better work management practices.
You get more work done with the same number or fewer people and manage work backlogs better. Wrench time is up to 52%, not the average of 31%.
For that to happen, you must get scheduled work done on time. More work had to be scheduled, it had to be fully planned, materials had to be available and there had to be fewer disruptions from unexpected breakdowns.
High performers do a better job of planning and coordination of material requirements.
They don’t schedule without plans nor without knowing materials are available. They suffer fewer breakdowns because they are doing more proactive work without over-maintaining. Doing too much of the wrong work can induce failures.
They rely more heavily on condition monitoring than preventive work. They know that relatively few failures are purely age or usage driven. All that translates to fewer shutdowns, fewer overhauls, fewer infant mortality failures and overall more uptime.
Choosing the right proactive maintenance approach requires thought about failure modes, their consequences and how they are best managed.
The best approach for that is Reliability-Centered Maintenance but there are other methods that work well too. For critical assets they use RCM, elsewhere, they use others methods.
High performers invested in planning, scheduling, materials coordination and RCM. They treat these as investments, not costs and that thinking had to grow.
Like many of us, many have gone through periods of running to failure in a break-then-fix operating mode. They struggled with lack of budget and a lack of cooperation from their operators. They had to find ways to justify the proactive spending.
They had to recognize that you cannot achieve these improvements by focusing only on one area of improvement.
Planning, scheduling, materials coordination, PMs, and RCM all work inter-dependently for best results – like a meal with many ingredients. Each ingredient provides some benefit on its own, but it is the combination that really delivers the best results.
Fixing one alone, like planning, won’t give you big savings. Similarly, don’t believe the hype that RCM is the answer to all your reliability woes. A CMMS will not deliver a high return on investment – it actually adds to costs. You need to take a balanced and gradual approach.
Use pilot projects to demonstrate that real returns are achievable while proving that you have a working plan for delivering more availability.
Focus on your worst performers first.
Improvements there can payback quickly and often help fund more improvements. You can usually do this within existing budgets by redirecting your budgeted funding from reactive repairs into PMs and the analysis needed to identify them but don’t forget that you also need to plan, coordinate materials and schedule effectively.
Confidence in your abilities is needed. Without it, you won’t take this risk of reallocating money within your budgets. If you won’t do that, then you probably don’t have what it takes to pull this off. After all, if you don’t believe you can do it, then why should anyone else?
Don’t try to be perfect
You won’t leap to top performance benchmark levels quickly. Target your initial efforts where payback potential is highest. Focus reliability improvement on your worst performers.
Plan the most commonly occurring jobs. Don’t fret about spare parts inventory levels or turns. That can come later.
The cost of downtime while you wait for deliveries is almost certainly greater than the cost of keeping parts on the shelf. Don’t try to be perfect. Be better tomorrow than you are today and continually improve.
It might take a few years to improve all the way to benchmark levels but all that time you are generating increasingly greater savings and earning potential.
At an electric utility, we achieved a 34% cost reduction over 8 equipment pilot projects saving almost $1M a year beginning in the next budget cycle.
That took us roughly 6 months from the start of training until the results of those analyses were put into practice. The cost for outside help was roughly $250k over that period. In a large mining operation, we achieved increases of 20% in production over a 6 month period. Revenues, in that case, were on the order of $100M.
The cost of that effort was only $750k! In both cases, waiting for the next budget cycle (and regulatory approvals in the case of the utility) would have been foolish. Cost control in the pure accounting sense wouldn’t have worked, but investing did.
Controlling cost is still important
Identify where you have real financial pain that is caused by equipment reliability problems and make those your first targets.
You probably don’t embark on major improvement programs all the time – get help from someone who does. Retired help from your own organization is probably the wrong way to get it.
No matter how good they may be, they really only know what you already know. You want new ideas and perspectives.
Other benefits will also show up in reduced safety incidents, fewer environmental non-compliance events (fines and cleanup costs), and more predictable business results (on-time delivery and meeting targets consistently), less capital investment (the older assets last longer), lower insurance premiums, improved quality performance, improved employee morale and fewer sleepless nights.
You probably can’t estimate these up front, but you can track them as you make your changes.
Doing the right maintenance, the right way and at the right time delivers value in many ways. Focusing only on maintenance costs to improving profitability will ultimately get you into trouble or prevent you from getting out of it.
Ill-conceived and poorly informed cost reductions often come in the form of reduced training, reduced headcount and less proactive maintenance – the only discretionary spending you can really “control”. But smarter managers know that by increasing some of that discretionary spending wisely will actually generate a reduction in non-discretionary spending on repairs.
Controlling cost wisely in maintenance is far more than an accounting exercise or the slashing of budgets.
Good maintenance cost control begins with a focus on how you can deliver the greatest value through the activities you control.
Conclusion
Focus on those that result in reductions in activities you don’t control directly. You can start now, within your current budget constraints, to deliver quick wins and savings.
You’ll need to look at planning, scheduling, coordination with your stores, your proactive maintenance program and reliability methods like RCM. It might seem like a lot to do but incrementalism, one method at a time, won’t work well. Hit all those areas gradually but in parallel, going after the “low hanging fruit” and you’ll find it is doable, even in tough times.
Leave a Reply