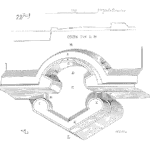
The cost of maintenance destroys your capital investment returns.
When equipment is first selected the buyer has the choice to buy for quality and long trouble-free operating life or to buy based on least cost. The least cost choice will result in high maintenance and operating expense for the life of the equipment.
When net present value cost of maintenance for cheap equipment is calculated in today’s dollars investors will discover that a large part of their capital will never earn them income but will be spent on maintenance and repair.
Keywords: replacement asset value, internal rate of return, opportunity cost
Overview
The cost of maintenance can send your business broke. If your annual maintenance cost is higher than 5% of your asset value you are in trouble.
The total maintenance cost depends on the quality of the equipment you use and how much maintenance it requires.
The smart business owner buys equipment that needs little maintenance and ensures that the business’ design, maintenance, operating and procurement policies and practices all work toward having long-running, long-lived, never-failing plant.
Where the Losses Arise
It is clear to any long-serving maintenance manager that the only policy that should be adopted in a business is to buy equipment that does not fail.
The cost of maintaining equipment is wasted money. Unfortunately, we are forced to live within the limits of our current technologies, and for the moment, that means we only have the option of buying equipment with parts and designs that require maintenance.
That being the case, it is smart business to look at getting equipment with a design that prevents failure and that requires little and simple maintenance.
In the chemical manufacturing industry, the world best practice maintenance costs are 1.8% to 2.0% of the replacement value of the plant (the original asset value incremented annually for inflation). In the worst operations, maintenance costs more than 5% of the asset replacement value per year. 5% represents $50,000 per year for every $1,000,000 of asset replacement value.
These organizations are unnecessarily wasting $30,000 a year for every $1,000,000 of asset value.
The effect of compounding the maintenance cost
Taken as an annual $30,000 sum and compounded over a twenty-year life at the business’ average weighted cost of capital (12% for the sake of the calculation) the total opportunity cost involved is $2,162,000.
This is money not earned over 20 years because it was spent on unnecessary repairs. If the $30,000 annual cost difference between 2% and 5% over 20 years were brought back to its present worth today (at the 12% rate) it would equal $224,000. This is $224,000 out of every $1,000,000 of asset replacement value not earning a 12% return because of poor equipment, poor design, poor maintenance and poor operating practices.
It is clearly a huge penalty for a business to pay because of inadequate design, purchasing, operating and maintenance policies and practices. The figures are even more astounding when put into tabular form on Table No. 1.
For each 1% of replacement asset value spent annually on maintenance over a 20-year period, $75,000 of every $1,000,000 of original capital will not return any dividend on the investment.
The best practice to adopt
You may have come across these words of advice before –
“It is unwise to pay too much, but it is worse to pay too little. When you pay too much, you lose a little money. When you pay too little, you sometimes lose everything, because the thing you bought was incapable of doing the thing you bought it to do. The common law of business balance prohibits paying too little and getting a lot – it cannot be done! So if you deal with the lowest bidder, it is wise to add something for the risk you run. And if you do that, you will have enough to pay for something better.” John Ruskin. 1819 –1900, English author, architect, and economist.
“There is hardly anything in this world that some man cannot make a little worse and sell a little cheaper, and the people who consider price only are this man’s lawful prey.” John Ruskin.
“You need to be rich to buy cheap products. Why? Because you eventually have to buy twice to have the job done properly.” Anon.
The best advice to every businessman is to only buy equipment that costs little or nothing to maintain. In fact, they should be demanding that original equipment manufacturers develop new technologies for their equipment to get maintenance cost down to nothing.
With less maintenance, machinery is available to operate for longer.
This translates into less spare parts, a smaller store, fewer operators, maintainers and fewer managers. The benefits gained from having reliable, long-lived plant extend well beyond just having lower maintenance costs.
If you are an investor then you may be better rewarded by putting your money into assets that require very little maintenance or into intellectual businesses that have few current assets.
If your business involves using equipment then it is critical that you buy top quality equipment requiring little maintenance.
Furthermore, you must employ able people and train them to become the best, most competent plant operators and maintainers you can possibly afford so that they can keep the plant running well and you are not wasting as much of your business’ capital money on maintenance.
Mike Sondalini
Editor
Feed Forward Publications
Website – trade-school.education
Annual Maintenance Cost as % of Asset Replacement Value | Current Replacement Value of Asset in $ | Annual Maintenance as Cost of Replacement Asset Value in $ without Inflation Effect | Length of Asset Life in Years | Weighted Average Cost of Capital % | Accumulated Value of 20 Years Maintenance Opportunity Cost at Average Weighted Cost of Capital Rate | Present Value of 20 Years Maintenance Opportunity Cost at Weighted Average Cost of Capital Rate without Inflation Effect |
1 | 1000000 | 10000 | 20 | 12 | 720524 | 74694 |
2 | 1000000 | 20000 | 20 | 12 | 1441049 | 149389 |
3 | 1000000 | 30000 | 20 | 12 | 2161573 | 224083 |
4 | 1000000 | 40000 | 20 | 12 | 2882098 | 298778 |
5 | 1000000 | 50000 | 20 | 12 | 3602622 | 373472 |
6 | 1000000 | 60000 | 20 | 12 | 4323147 | 448167 |
Table No. 1. The Net Present Value of the Cost of Maintenance
We (Accendo Reliability) published this article with the kind permission of Feed Forward Publishing, a subsidiary of BIN95.com
Web: trade-school.education
E-mail: info@trade-school.education
If you found this interesting you may like the ebook Centrifugal Pump Problems & Answers.
Mike
We might be on the same page when we publish or post about awareness of price vs performance.
You have used some quotes that I would I like post to my Linkedin groups. Permission to use?
Hi Alex,
You may excerpt quotes if you provide Mike full attribution and link back to the article
cheers,
Fred