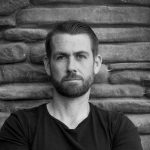
In one of my recent webinars on ‘reliability culture,’ I was asked a really good question. Someone (let’s call him ‘Tim’) asked me:
How do I get the most out of my ‘ad hoc’ reliability team?
Tim had recently created a ‘reliability team’ made up of people from different areas of his organization. These people were smart, qualified, but had non-reliability engineering day jobs. They weren’t qualified reliability engineers. They weren’t idiots. And they couldn’t devote all their time to reliability.
The were the typical ‘ad hoc’ reliability team. Many organizations want to improve reliability, but don’t have the resources to build a fully staffed reliability department in the next 30 minutes. So what can they do with an ad hoc team?
Well, for any organizational endeavor I suggest the following concepts, in this order:
1. why
2. value
3. how
4. create
5. what
The ‘why’ of a large organization or a small team is its most important element. Is the ‘why’ of a big organization to image each square inch of the earth’s surface daily? Is the ‘why’ to relentlessly focus on the customer experience of an online marketplace? These are two real-life examples of very successful companies.
So ‘why’ is your ad hoc reliability team needed in the first place? Is it to have everyone trained on the ‘vital few’ reliability activities that pertain to their jobs? Is it to improve the visibility of reliability performance? Is it a short-term goal that will be updated once it is achieved?
Whatever it is, the ‘why’ needs to define what success looks like. If you don’t have a ‘why,’ ad hoc reliability teams quickly descend into pointless monthly meetings where people compare notes and otherwise admire reliability problems.
The next concept is ‘value.’ Is your ‘why’ going to add ‘value?’ Training your organization on how to present reliability graphs might be nice … but does this help make better decisions? If it doesn’t add value, then your team is focused on a hobby. Hobbies quickly become despised by everyone else for the useless imbuggerance they are.
So don’t rush thinking about these concepts. Take the time to really understand the value you are hoping your ad hoc team will generate. It might mean you need to revisit your ‘why.’ Maybe find another ‘why’ that is even more valuable.
Getting this right makes the next concept easy – working out the ‘how.’ Perhaps your ad hoc team’s ‘why’ is all about driving down manufacturing defects in a specific component because that represents the most ‘valuable’ reliability endeavor for your organization. Isn’t it a lot simpler to identify potential steps when you have worked this out?
‘How’ you do things. Training. Procedures. Test chambers. External support. Guidebooks. They all tend to fall out of a considered process to identify a ‘valuable why.’ The act of ‘creation’ is simply your now empowered employees implementing the ‘how.’ And because you have an articulate ‘valuable why,’ everyone knows why they need to complete this new course or follow that new guideline. In other words, they are motivated.
The ‘what’ is the outcome of all of the above. The quality manufacturing process. The easy-to-use reliability visualization tool to help everyone see how we are going. Whatever it is, this process of ‘creating’ your ‘what’ is smooth, simple, and rewarding. All because you started with ‘why.’
So before you do your next amazing ‘reliability thing’ … tell me what your ‘why’ is?
Leave a Reply