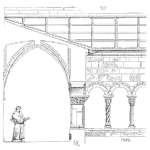
Creating a reliable product that meets customer expectations is risky.
What is risk and how does one go about managing risk? The recent set of ISO standard updates elevates risk management.
A starting place is a definition. [Read more…]
Your Reliability Engineering Professional Development Site
by Fred Schenkelberg 2 Comments
Creating a reliable product that meets customer expectations is risky.
What is risk and how does one go about managing risk? The recent set of ISO standard updates elevates risk management.
A starting place is a definition. [Read more…]
by Fred Schenkelberg 2 Comments
Benchmarking is the systematic process of observation and analysis.
The evaluation of a project, method or process best practices as performed by recognized industry leader may reveal improvement opportunities for your organization.
Benchmarking may focus on diverse business processes and with both internal and external subjects.
The intent is to understand what makes the subject’s process work well.
Understanding a system that operates well may reveal the elements in your process that may benefit with a change.
Keep in mind that not all best practice processes may apply to your specific situation. (Lapide, 2005) [Read more…]
by Fred Schenkelberg Leave a Comment
Image that. Customers say one thing and expect something else.
A customer may provide a detailed and complete reliability specification, then, 6 months into using the product complain it is not reliable enough. [Read more…]
by Fred Schenkelberg Leave a Comment
Warranty is a part of doing business. Warranty management is not just the terms listed on the box.
Understanding the entire warranty process, along with your options, permits you to manage your warranty, rather than the other way around.
This is a short overview.
Pieces of a warranty program occur well before the first product ships and may affect the company bottom line for years after you ship your last product.
Brand promise, marketing, finance, customer service are not common areas for a reliability engineer.
Yet, the impact of product failures tends to dominant warranty expenses.
Therefore understanding the many elements around warranty management is essential for any reliability engineer. [Read more…]
by Fred Schenkelberg 1 Comment
The offered warranty is an internal part of many purchase decisions, plus many business models.
While obligatory to offer a warranty, especially for consumer products, the specific terms, duration, and eventual total cost of honoring warranty claims may vary dramatically.
One key to managing the overall warranty expense is to estimate the potential future warranty claims, followed by accurately tracking actual expenses during the warranty period. [Read more…]
by Fred Schenkelberg 1 Comment
Concurrent engineering is a common approach that pairs the development of the product design and it’s supporting manufacturing processes through the development process.
Design engineers may require the creation of new manufacturing processes to achieve specific material properties, component performance, or mechanical, electrical or software tolerances. [Read more…]
by Fred Schenkelberg Leave a Comment
A product or system’s actual reliability performance is a function of the design, assembly, and use.
Decisions made during design predominately create the inherent reliability capability performance.
The selected components, manufacturing, transportation and installation all can add variability and errors to the product, often reducing the actual reliability performance.
The use conditions and maintenance add another layer of variability, again reducing reliability capability. [Read more…]
by Fred Schenkelberg Leave a Comment
System engineering is a superset of the other engineering fields (mechanical, civil, electrical, software, etc.) as the system engineers work to bring all the various elements of a system together into a final and cohesive whole. [Read more…]
by Fred Schenkelberg 1 Comment
The software element of products continues to grow.
Likewise, the number of field failures due to software issues continues to grow. Writing code is relatively straight forward, and some may even say it’s fun.
The process of debugging, or finding and fixing software defects, is not fun. [Read more…]
by Fred Schenkelberg Leave a Comment
Just asking a customer how reliable they want your product often provokes an honest answer. The customer, and you most likely, do not want any failures.
Failures are troublesome or in some cases dangerous.
You and your customers realize that not every unit produced will operate over a long and useful life. There is some chance that something will fail. The definition of ‘some’ is often vague. [Read more…]
by Fred Schenkelberg 1 Comment
The reliability engineer may have many roles within an organization.
You may be specialized and focused only on the analysis of field data. Or you may be a member of the organization’s strategic leadership team.
You might support one or more product development teams, or work with a team of reliability professionals supporting just one subsystem. [Read more…]
by Fred Schenkelberg Leave a Comment
Ethics relate to the moral correctness of a person’s behavior given the groups moral principles.
Society, in general, has a set of standard expectations to guide our behavior. This includes fundamentals such as not harming others or behaving in a deceitful manner.
Religious, professional and informal ‘codes’ document the set or principles which guide our behavior in line with moral correctness. [Read more…]
by Fred Schenkelberg 2 Comments
Each organization creates their own version of a product life cycle.
Often there are phase gate reviews that signal a transition from one phase to the next. In general, each set of phases follows a common progression from idea to retirement.
There are many references that include a description of the life cycle phases, so let’s explore two of them. [Read more…]
by Fred Schenkelberg 1 Comment
Embarking on a product development project contains many aspirations, including that the product should work as expected.
The device functions and does so over time. Enough time for the customer to deem the device reliable.
That is one way to approach setting a reliability goal for a project. Estimate what will delight the customer. Set a target for how long without failure your new design function.
The goal provides a focus for the team. [Read more…]
by Fred Schenkelberg Leave a Comment
A common question concerns the warranty period.
How long should we, the manufacture guarantee that our product will work as expected? Do we include limitations or not? How do we decide? [Read more…]