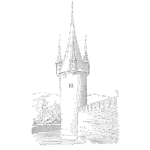
Guest Post by James Kline (first posted on CERM ® RISK INSIGHTS – reposted here with permission)
How a Cultural Audit Can Assist Risk Management
Introduction
An organization’s culture is an important determinant of its success or failure. This is because an organization’s culture is the combined effect of the employees’ underlying assumptions, beliefs, attitudes and expectations. Each can affect performance and adaptability. A cultural assessment can help determine areas that can inhibit mission accomplishment. This article lists the different techniques used in conducting a cultural audit and indicates how it can help guide corrective action.
Cultural Audit
Cultural Audits are based on a set of organizational characteristics that support attainment of the organization’s mission. The steps of the audit include instrument selection, data collection, data analysis and the identification of relevant policy options.
The instruments used include focus groups, surveys, interviews and direct observations. Using multiple instruments is recommended. Focus groups tend to concentrate on the culture of the organization. Surveys are generally designed to identify the degree to which behaviors align with organizational policies. Interviews seek employee opinions on specific issues. Exit interviews, for instance, focus on why the employee is leaving the organization. Observations seek to determine actual behavior.
While cultural audits can be conducted in house, consultants using standardized instruments are often hired. An example of such a standardized instrument is the Gallup Q-12. It is conducted by the Gallup organization. The Q-12 is a cultural survey used by 400 organizations. Because of its broad use, a comparative analysis can be informative. An example is the United States Postal Service (USPS).
United States Postal Service
A 2015 Q-12 determined USPS scored in the 1st percentile. Compared to the other 400 companies using Q-12, USPS is at the bottom. USPS employees said they rarely receive recognition for good work; their supervisors don’t care for them as people, they don’t feel their job is important; they lack opportunities to learn and grow, and their fellow employees are not committed to doing quality work.
The USPS career employees’ attitudes coincide with the reasons non-career employees are leaving. Exit interviews indicated the reasons for leaving as: 1. Lack of schedule flexibility, 2. Don’t like the supervisor, 3. Physical demands, 4. Too many hours and 5. Not enough hours.
The turnover rate for non-career employees is 42.7%. Non-career employee turnover costs the Postal Service about $95.1 million a year. High turnover is not only expensive, but it can inhibit the accomplishment of the postal mission.
The two survey results indicate that there is low morale. There is also a shared opinion about the supervisors. Based on this information policy actions can be devised to address specific aspects of the problem, such as turnover, as well as, the underlying cultural issues. Once the policies are put forth, an assessment of any risks can be conducted.
Conclusion
An organization’s culture is a key determinant to its ability to carry out its mission. A cultural audit is a technique used to assess that culture. It is designed to identify where the attitude and behavior of employees and management may inhibit the accomplishment of the organization’s mission. Once problem areas have been identified, policies can be devised to remedy the problems and any risks associated with the policies assessed.
Reference
McCoy, Shawn, 2016, “Exclusive: Survey Finds Turmoil In Postal Workforce” InsideSources
April 28, http://www.Insidesources.com/category/politics/
Office of Inspector General United States Postal Service, 2016, “Non-Career Employee
Turnover”, Report Number HR-AR-17-002 December 20, Washington D.C.
Solomon, Cynthia, 2004, Culture Audits: Supporting Organizational Success, ASTD Press,
Alexandra VA.
Bio
James Kline is a Senior Member of ASQ, a Six Sigma Green Belt, a Manager of Quality/Organizational Excellence and a Certified Enterprise Risk Manager. He has over ten year’s supervisory and managerial experience. He has consulted on economic, quality and workforce development issues. He has also published numerous articles related to quality in government and risk analysis.
Leave a Reply