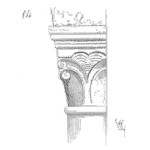
Image that. Customers say one thing and expect something else.
A customer may provide a detailed and complete reliability specification, then, 6 months into using the product complain it is not reliable enough.
They want the device to
- Last longer
- Have more features (and cost less)
- Survive harsher environments
- Operate more often
- Fail less often
Maybe we need a fifth element to the reliability definition. The expectation will increase over time.
The demand to create more reliable products will continue.
Product family after product family has seen the pattern of increasing expectation around reliable performance.
Understanding customer expectations
Whether part of the customer requirements or ascertained via surveys, the process to define what customers actually want concerning reliability is difficult.
Customers often do not know what they really want till they have the product and experience its reliability performance.
Even then your customers may not be able to articulate what they really want beyond, “make it more reliable.”
In the process to understand your customer’s reliability objectives, include a bit of forward-looking consideration.
Increase the reliability targets for your products a bit beyond your customer’s initial desires, if possible.
This has the benefit of adding a little margin over the initial expectation, plus provides a little room into the future to meet the unstated increased reliability expectation.
Customers rarely desire something that is less reliable.
Setting reliability goals
The reliability goal for your product has for elements:
- Function
- Environment
- Probability
- Duration
When setting the goal for the internal specifications, consider all four elements.
Increase the goal for each just a bit to help your team design a product that meets the current and future reliability expectations.
Function – include the ability to evaluate and monitor via reliability testing as many functional elements as possible.
This includes the primary core functions, of course, plus, the secondary functions such as color fastness of the enclosure.
The ability to evaluate the risks and measure reliability performance over time requires understanding how every function may fail.
Even a minor functional failure may taint your customer’s perception of the reliability performance.
Environment includes two parts.
First the weather or the surrounding conditions affecting your product. This is more than temperature and humidity. Include stress factors that may cause acute or systemic paths to failure.
A drop of sufficient height may shatter your product, yet a modest vibration may degrade the performance over time.
Both are important to consider.
One technique to catalog all the environmental stresses is to image a ‘day-in-the-life’ of your product.
Power, weather, radiation, insects, etc. Each has a means to destroy your product.
Another element of environment is the duty cycle of your product.
Some products are in service a few times a day, while others have a full-time duty cycle. Even the full-time systems my experience different loads during the day (causing cycling damage).
Consider how the loading and the operating time may increase in different situations.
Probability and duration should be set in pairs and either or both may require increases to meet future expectations.
If your product reliability goal includes an initial requirement to be at least 95% reliable over 1 year, you may expect customers will quickly require 98% reliable over 2 years.
Life testing and modeling are already difficult, now I’m suggesting you consider increasing your targets.
It will only pay dividends as your customer expectations increase in the near future.
Summary
Reliability expectations are a moving target.
Use the concept of windage to aim a bit higher to accommodate the shifting nature of your customer’s expectations. Aim higher.
Have you been surprised by your own or your customer’s reliability expectations?
Have you had the conversation around that current product meets the old requirements, and now we want more reliability?
Share your experience in the comments section. Let’s share how the process of goal setting actually works.
More content on the topic of changing reliability expectations
SOR 187 Customer Reliability Expectations Change Over Time (podcast)
Leave a Reply