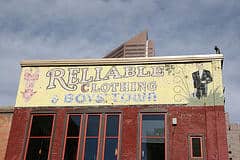
How do your customers talk about reliability
And, what can you do about it?
As engineers laying out a factory or designing a new product we have to meet the reliability expectations of our customers. It would be great if the system would not fail or need repair, yet that is often not the case.
In most circumstances we know as do our customers that failures will happen. It is finding the right balance between reliable performance and expectation that is difficult. In some cases it is the language we use to talk about reliability with our customers that leads to the confusion.
Advertising Use of Reliability

A common use of the term ‘reliable’ or ‘reliability’ is found in a wide range of advertising. Businesses use the term in their name. Reliable Cheese Co. (now closed) being one of my favorites. Reliable Movers on the side of a moving van caught my eye once. Not sure if was the name of the company or a slogan.
The definition of reliability used in advertising is not the same as the technical definition we use in engineering. It means dependable, trustworthy, operate as expected, or loyal. Often not something we can quantify or measure directly.
The terms reliable and reliability are used in advertising precisely because the common definition implies something of value. It is widely used by brands to associate the brands products with the good trait of reliable. The simple act of declaring a system reliable is like saying you enjoyed a particular movie. It is subjective. Using the common definition of reliable, what I call reliable may or may not fit your definition. That is why there exists a stricter definition for reliability found in many reliability engineering texts and courses.
Reliability for Engineers
We define reliability as the ability of a system to perform as expected in a given environment with a specific probability of success and over a specified duration.
Other’s said this more elegantly, yet all the definitions have four elements:
• Function
• Environment
• Probability
• Duration
For example a cell phone goal may read as:
• The cell phone should make/receive phone calls (function)
• As an indoor/outdoor portable device (environment)
• For two years with a 95% probability of success (duration and probability couplet)
Is this what your customers say when talking about their reliability expectations? Probably not.
Customers and Reliability
Our customers think about reliability as the advertising agencies do – not as reliability engineers define reliability. When a customers says or expects the product is reliable they generally do not have 98% over 2 years in mind. They believe the product will work as expected for as long as they expect it to last. This is not well defined.
When pressed (ask them what they mean) your customers may talk about wanting a product
• That just works
• That lasts a long time
• That works long enough to provide a return on investment
• That works for 2 years
Some customers may ask for a specific MTBF value or better, others may ask for no failures over 5 years, and an occasional customer may ask for better than 98% probability of success over 2 years.
Translating Reliability Expectations from Customers to Engineering
Unless you have the customer that provides a complete reliability specification, you will have to translate. Start with the conversation around what they really want. If a product has a small chance of failing over two years is that good enough? If 20% fail in the first year, is that acceptable? Bracket and narrow down the range that is acceptable to your customers.
What duration is important and should be part of the discussion. For cell phones maybe two years is good enough for a relatively small chance of failure. After two years many customers upgrade anyway. Also, after two years the customer may feel they have received the full value from the purchase.
Two years is not good enough for a car though; or, washing machine, or automated bottling system.
The right probability and duration is largely a factor of customer expectation and technology capability. It may take some market research and life testing to determine the right balance.
Early life and wear out
Besides the expected useful life of a product, there is the new car smell and wear out expectations, too. A new product should just work out of the box, it should smell good. If it fails early it has the highest chance of damaging the brand and customer loyalty.
Products wear out and eventually fail. How large is the market for cell phones that last 5 or 10 years? If the long term use is important you may want to invest in the long term life of the product. Some products have very long life expectations. Implanted medical devices and solar panels should last 20 or more years.
Striking the right balance
With market research, customer conversations, and technology capabilities we are ready to create a reliability goal that balances the desire to not have product failures, profit, and customer value/satisfaction.
It is a balance and not a fixed solution. Did I mention the fifth element of reliability specifications? It is customers will continue to want:
• More functions
• Harsher environments
• Lower probability of failure
• Longer durations
It’s funny. And, we all want our systems to cost less. That is why we’re in engineering, to invent the systems that meet or exceed customer expectations. Adding reliability, well defined reliability, to the mix just makes sense.
Leave a Reply