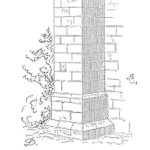
Customer Usage Switch Verification
Here is an example of a common engineering development task. A design engineer needed a life test plan for a switch verification in a safety system. We jointly developed a plan by taking a system view of the component function, considered corporate and regulatory requirements, customized it to the supplier’s test capabilities, executed the plan, and made design changes to remove product defects.
Regulatory Requirements
Federal automobile safety requirements mandate systems that protect pedestrians. A vehicle with a manual transmission must be prevented from surging forward or rearward when the engine is started.
Engine Starting
A powertrain controller was responsible for starting the engine. It enables a engine starts only if the clutch pedal is fully depressed, meeting the requirement. An electrical switch was developed that sensed when the clutch pedal was fully depressed, and provided a signal to the engine controller. Since the switch was new, a verification life test needed to be developed.
Corporate Requirements
The factors used to develop the validation test included,
- The corporate verification target for safety systems was 10 years or 100,000 miles of customer usage.
- The safety system reliability verification target was a minimum of 95% reliability with 90% confidence.
- No test failures were permitted below the 95th percentile customer usage.
Switch Cycles
The switch was mounted in the clutch bracket and it’s electrical contacts closed when the clutch was fully depressed. The design engineer expected the main failure mode would be electrical contact wear and thus cycle related. The switch cycles were expected to be mileage related. The first step was to define the distribution of clutch cycles in 100,000 miles of customer usage. A review of older product specifications yielded targets of 500,000 and 2,000,000 cycles. As the basis for these targets was unknown, we developed a specification based on clutch cycles from a Customer Duty Cycle Handbook. This contained the results of vehicle studies that showed the 95th percentile clutch usage was about 850,000 cycles in 100,000 miles at 90% confidence.
The “Laugh Test”
I always ask if the proposed target is reasonable. Who will operate a clutch 850,000 cycles in 100,000 miles, about 8.5 times/mile? Consider a vehicle in a major urban center, like New York City, continually used in heavy traffic? At the time, most manual transmissions had 3 or 4 forward gear positions. When a vehicle is accelerated to normal road speeds, the clutch is used to shift the transmission into successively higher gears. Similarly, when decelerating, the clutch is used to shift the transmission to successively lower gears. If a vehicle is is operated where it achieves normal operating speed and then comes to a stop, then the clutch is used to shift from neutral to 3rd gear and back down to neutral, resulting in 6 cycles. Other partial shift patterns are possible. All can occur in a mile of travel, so 8.5 cycles/mile is was judged to be reasonable in a crowed urban environment. The 850,000 clutch cycles was was duplicated in the switch and was accepted as a test bogy for a 95the percentile usage.
Test Strategy
The switch, as part of a safety system, had a corporate reliability verification testing target of R95/C90 (95% reliability at 90% confidence). Using a success run criteria for testing to a bogy with 0 failures allowed, the required sample size was 44 parts. Unfortunately, the supplier’s test fixture could test only 12 parts at a time. One approach would have been to divide the parts into 4 groups, each tested to 850,000 cycles. The test fixture would be occupied for about 3,400,000 cycles. Since switch failures were not allowed, any switch failures would result in more test-and-fix actions and more test cycles.
Instead an extended life test strategy was selected that would use 12 parts, cycled to 2,200,000 cycles. Failures would be allowed if they occurred after 850,000 cycles and if analysis indicated that the corporate target of R95/C90 at 850,000 cycles was satisfied. The advantages of this test plan included reduced sample sizes, checking for wearout beyond the test bogy, shorter fixture time, and an opportunity to root cause switch failures.
Test Results
The first failure was a broken spring at 650,000 cycles. The spring experienced a fatigue failure, which was removed by changing the spring design to reduce stresses. The switches continued to be tested and another occurred at 2,200,000 cycles. The spring showed wear marks from a plastic shaft that prevented column buckling of the spring. The shaft was constructed from a glass filled plastic. It was proposed that sharp edges on the glass filler abraded the spring, so the glass was removed from the plastic shaft. After these product changes, a final set of parts was tested to 4,000,000 cycles without failure. The switch was put into production without any safety or warranty issues. The costs of these design changes were minimal so the switch price was unchanged.
Conclusion
- Verification testing targets can be based on customer usage.
- Applicable corporate and regulatory requirements must be satisfied.
- Extended life testing reduced total test time and sample sizes.
- Extended life testing provided an opportunity to search for failure modes beyond the test bogy.
- Root cause analysis of failed parts identified design weaknesses.
- To eliminate failure modes, low cost design changes may be effective.
Leave a Reply