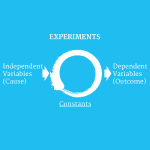
Design of Experiments (DOE) is a phenomenal way to identify key relationships between variables and effects. It fully leverages statistics to not only identify these relationships in a compressed time frame but any “interactions” between variables that cause a specific effect. These interactions would not have been observed if experimentation was limited to adjusted one factor at a time (OFAT).
Traditional experiments focus on one or two factors at a couple of levels and try to hold everything else constant, which is impossible to do in most processes. When Design of Experiments (DOE) is properly constructed, it can focus on a wide range of key input factors or variables and will determine the optimum levels of each of the factors. If it is unclear which variables contribute the most to the design sensitivity, then it is time to run a DOE to make this determination. In most designs, there are factors that you can control and other factors that are beyond your control. Use a DOE approach to
- Determine which factors are controllable, and
- Help find the optimal balance between each of the factors. This will yield the most robust design possible given the factors present.
Here are a few benefits of a DOE:
- You can evaluate many factors simultaneously, making the DOE approach economical.
- Sometimes you can’t control factors that have an important influence on the output (noise factors), but you can control other input factors to make the output insensitive to noise factors.
- It isn’t necessary that you have in-depth, statistical knowledge to get a big benefit from standard planned experimentation.
- You can look at a process/design with relatively few experiments. You can distinguish the important factors from the less important ones. You can then concentrate your effort on the important ones.
- If you overlook important factors in an experiment, the results will tell you they were overlooked.
- You can run precise statistical analysis using standard computer programs.
- You can improve quality and reliability without a cost increase (other than the cost associated with the trials).
The common language associated with the DOE process:
- Array—a table in which the factors are across the top (horizontal axis) and the number of runs is on the left side (vertical axis). The size of the array is chosen based on the number of factors and levels.
- Controllable factors—all the factors that you have the ability to change.
- Effects or response—dependent variables (output variables).
- Factors—independent variables (input variables).
- Interaction—influence of the variation of one factor on the results obtained by varying another factor.
- Levels—value at which the factors are set.
- Main effects—the effects of the factors.
- Noise—effect of all the uncontrollable factors.
- Uncontrollable factors—external factors that you don’t have the ability to change.
After choosing the DOE you would like to run, here are the steps involved:
- Select the Factors and Levels
- Assign Factors to the Array
- Substitute Values into the Array
- Calculate the Mean Square Deviation (MSD) and Signal-to-Noise (S/N) Ratio
- Determine the Correct Combination
- Build the S/N Response Table
- Choose the Significant Factors
- Run Additional Experiments, If Needed
-Adam
If you are interested in learning more about DOE take a look at chapter 9 of “How Reliable Is Your Product? 50 Ways to Improve Product Reliability” available on Amazon in hardcover and Kindle.
P.S. I threw in a fun example of a DOE using baking cookies as an exercise in the chapter… Group training session at work on Friday afternoon?…just saying.
Leave a Reply