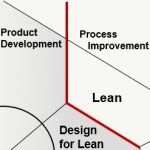
In this article series, we covered several topics in the area of product development and project management. We will now begin to explore process improvement with the topic “Design for Lean”. While design for lean may be a subtopic within product development, it helps us understand operational risks, operational costs, enables operational planning and process improvement.
An operational process is required to commercialize any product (or service). Accordingly, the future state operational process can be characterized with a foundational lean tool: the value stream map (VSM).
A value stream map provides a graphical representation of the value chain to the customer. A simplified representation of a VSM is provided as follows:
- The example above is a manufacturing value stream map with information flow across the top and material flow across the bottom. Information flows right-to-left (from the customer) and material flows left-to-right based on demand (pull from the customer).
- Note that a value stream map can be any process map that includes data. Even an information flow map for a transactional process (such as a swim lane map) can contain data which characterizes the process both graphically and analytically.
- The process starts with understanding demand from your customer, and then identifying the process flow by working backward through the value chain. What is the last step before the product is received by the customer? The step before that…and so on.
- Collect or estimate data for each process block. Data might include cycle time, # of resources, # of workstations, machine up-time, etc. Ideally, historical data would be available from a similar value stream within your company. If no data is available, the VSM can still be used to contribute to your data collection plan. Note that product cost is a function of the future state operation process, therefore cost and margin estimates can be supported by VSM data. Where are your operational costs the highest and what mitigation actions should be taken? Are there actions that can be taken now (in the design process) to reduce the cost of our operational process?
- Regarding the information flow from the customer, how will the demand from the customer be received and distributed through the value chain? Will there be operational planning, batch processing or a ‘push’ system? Is there an opportunity to establish pull signals, supermarkets and/or kanbans?
(Note that future articles will provide more details on VSM and lean manufacturing.)
Recall our foundational objective for our customer is to maximize value and minimize cost. This includes providing a product that has value as well as a manufacturing (or operational) value chain that makes value flow at the pull of the customer and minimizes waste. The sooner we understand the future state value chain in the product development process, the better.
Let’s consider a couple of examples:
- A sterilization process is established for an internal subassembly of a prototype medical device, and becomes an ‘official’ part of the FDA-approved process. The subassembly must be packaged, shipped, sent to an external supplier, sterilized, received, removed from packaging and re-introduced into the manufacturing process. A future state value stream map would have revealed the impact of the decision on cost and lead-time. Additional up-front investment in R&D might have enabled this sterilization sub-process to be avoided, thereby significantly reducing costs and improving product margins.
- A makeshift IT system is created which enables traveling nurses to visit skilled nursing facilities outside of scheduled time with patients. However, an IT resource must manually load data each morning, before the nurses scheduled visits. While the internal customer is pleased with the immediate impact of the service, manually loading the data late at night (every night) is a less-than-ideal operational process, especially if more semi-automated processes are added.
In these examples, the scope of the project may have been minimized, however, with a costly impact on the operational process. During the design phase of your product development process, consider a value stream map of your the future state to validate and model your operational costs. As your operational process becomes more mature, the VSM can be updated and analyzed on an ongoing basis for continuous improvement.
Hi Robert:
We would like to reprint this article in CERM Risk Insights. Fred and I routinely swap pieces.
This is a valuable piece to our readership. Much thanks for consider this request. Best,
Greg Hutchins
Greg,
Feel free to reprint and thanks for your interest…!
Rob Allen