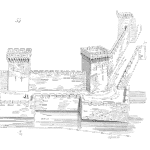
Testing a new design is expensive and takes time to accomplish. During the design, process engineers make assumptions across many decisions. Unknown interactions and unanticipated events may lead to product failure.
Finding design weaknesses early in the design process permits the team to address and correct problems.
Discovering the weaknesses is one way to provide evidence that the design team’s set of assumptions are justified. It also helps the team gather information on areas that have plenty of design margin and those areas with little or no margin.
There are four basic approaches for discovery testing:
- Margin tests
- Sample size of 1
- HAST (highly accelerated temperature and humidity stress test)
- HALT (highly accelerated life test)
Margin tests
Design engineers have used safety margins to account for the uncertainty around the variability of:
- Material
- Assembly
- Load
The safety margin means the design is stronger than the expected loads. You may have heard of a 1.5x or 2x safety margin. A 2x margin means the design is twice as strong as the expected load.
Margin testing simply exposes the product to the stress at the margin. So, let’s say a system is expected to see a maximum ambient temperature of 50°C. If the safety margin is 1.5x, then the design team would create a product that would operate at 50 x 1.5 = 75, or 75°C.
Margin testing in this simple example would expose a few products to 75°C and evaluate their performance. Generally, margin testing uses one stress variable at a time.
Sample size of 1
In some cases, we only have one sample available for testing. Examples would be railroad engines or manufacturing equipment. Generally, these are complex and expensive items.
In this case, discovery testing is one with some forethought. Initially, make sure the unit works as expected under normal operating conditions. Then step up stress to the maximum stress levels. If all is still working. Focus on major components that could be replaced within the system and continue to increase stress on those elements.
Continue to add stress taking the system to the safety margin levels, again one stress at a time (typically).
Take care to plan the testing from lower to higher stresses, and work from least likely to cause failure to more likely when applying stresses.
Finally, if possible, continue the application of stress till failure. Learn as much as possible. Any statistical analysis is fairly meaningless, yet knowing the product as designed and built can work across the expected range of conditions, with margin, plus knowing what will fail all provided meaningful information back to the design team.
HAST
According to Mil HDBK-338B HAST or highly accelerated temperature and humidity, stress testing evaluates electronic components.
Given the lack of connection between failure mechanisms to the applied stress for most components, this test should be done only once a relationship between the applied stress and time to failure has been established.
Following just the standards provided test time most likely will not result in failure. This does not provide meaningful information back to the component design team. Thus, I recommend continuing to test longer or with increasing stresses to force failures to occur.
HALT
Highly accelerated life testing is most likely the second worse four-letter acronym in our profession. Yes, this approach to testing is highly accelerated although the actual acceleration factor is unknown. It does often result in product (multiple) failures, yet does not provide an estimate for product life. And it is not a test that can be passed.
HALT is an exploration of a product design to find design weaknesses. The process includes applying single then multiple stresses in increasing steps until failures occur.
It does not require a HALT chamber although the combined temperature and vibration chambers are very useful for many electronic based products as temperature and vibration precipitate many failures in electronics.
HALT is a development tool to find weaknesses permitting the design team time to solve the problem. It should be done early and often in the design process.
Summary
The four approaches are not the only ways to discover problems with a design, yet they do provide meaningful information quickly. During a design, the process time is often in short supply thus evaluations like HALT have become very popular.
Related:
Program Elements Part 2 (article)
ALT and HALT (article)
Reliability Testing Considerations (article)
Leave a Reply