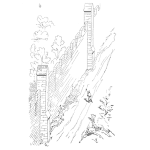
This activity-based costing (ABC) method calculates the actual cost of a failure incident and uses the total dollar value to the business as the means to rate equipment criticality. The criticality of an item of plant is determined by the cost consequences and losses of equipment failure across the whole company. Using this method puts a real dollar value on a production equipment loss incident. This financially robust and reliable method provides an accurate way to prioritise production equipment and to justify the necessary risk management and maintenance measures to protect against failure. It recognises that a production failure event has cost repercussions throughout an organisation affecting many people and departments, with all of them incurring costs. These costs are lost business profit that could have been earned and banked, but for the incident. The financial model reflects the actual production and maintenance practices in the operation and their cost implications to the whole organisation if they are inadequate. It delivers clear indication of the responsibility’s managers, supervisors, operators, and maintainers have of properly running, maintaining, and caring for plant and equipment to prevent production-losses to the business.
Keywords: equipment criticality, activity-based costing, equipment failure, operations risk management, production-loss management, operating cost control, maintenance strategy
What is Equipment Criticality?
Equipment criticality is used to identify operating equipment in a priority order of importance to the continued operation of a facility. The priority ranking is decided by the operating risk from equipment failure. Those equipment items that will stop production if they fail are identified as critical. Higher levels of maintenance and operator care are given to those items to maximise their level of reliability.
An entire facility’s plant and equipment are rated on this risk priority scale, after which maintenance strategies are matched to the equipment criticality. The same method is then applied to the assemblies and components within individual items of plant and equipment to identify which parts are critical to its continued operation. Again, the necessary maintenance is then matched to the importance of the item to the operation of the equipment.
A sample ‘Equipment Criticality Rating’ for a small family car might be as shown in Table 1. The table is not a complete analysis of a car, as the subcomponents can be further split into sub-sub-components, and their priorities also determined. The simplicity does not prevent us from seeing how the equipment criticality rating process is applied and noting what benefits arise from using it.
Typically the equipment’s criticality is arrived at by a competent group of people formed to analyse and categorise each item of plant. The review group consists of the operators of the equipment, the maintainers, and its engineering designers. Where such people are not available then competent equivalent people are used who know the equipment well.
Drawings of the facility’s processes showing every item of plant and equipment are used in the review. Equipment by equipment the group applies the RCM method and asks the consequences of failure to the operation. The envisaged severity of the failure is used to categories criticality.
Once the criticality of the equipment is set, a matching minimum level of maintenance is specified for it. The critical items to the operation get sufficient and appropriate maintenance and monitoring to keep them as reliable as is required. Those items that can cause inconvenience are also given the amount and type of maintenance suitable to their situation.
The group doing the car criticality analysis would consist of car mechanics, car drivers and car designers would have taken drawings of our family car and, assembly by assemble, identified what equipment failures were possible and the effect each failure would have on the use of the car. Each person would have contributed what they were competently able to advise and recommend at each stage of the review. The effects of a failure can be either total loss of car usage, partial loss of a system but the car could still be used, or no effect from the failure on the use of the car.
The failure effects are recorded in a table along with the recommended means to prevent each failure from happening. The selection of the table column rating headings is flexible and based on a suitable criticality scale for the situation.
The example of Table 1 was arrived at by using standard risk-based equipment criticality rating methods. The risk equation, Risk = Consequence ($) x Likelihood (events/year), was the basis for theriskanalysis. Thegroupdecidedtheoperatingconsequenceoffailureanditscollectivehistory determined the likelihood of failure. It used past equipment failure history to envision possible future failures and to identify failure modes. After which expert opinion is given by the group on what maintenance to do to prevent the failure modes arising.
The Problem with Standard Criticality Decision Methods
There are a couple of short comings with using standard equipment criticality rating methods.
The priority rating decisions from standard criticality rating methods are opinion-driven and are not based on real consequences of a failure. They only consider operating cost impact and do not identify the true and full failure costs suffered by the whole organisation. As a consequence, the business-wide risk is not properly analysed, and wrong risk control strategies are selected.
The rating of an item at a certain level of criticality using standard criticality rating methods is the result of knowledgeable people making an informed decision based on their understanding of the consequences of a failure. Since the review group consists of several people with different experiences and perspectives it is the practice that the final arbiters of the criticality choice are the persons operating the equipment. As it will be they that must live with the consequences and costs of failure, it is they that make the final decision on how it will be addressed and how much cost they are willing to accept.
This type of priority selection process is open to unintended error from misunderstanding and limited knowledge. Because it involves subjective decisions based on past experience, it is possible that a person’s experience is not deep and broad enough to make the better choice. They may be overly conservative and make an item totally critical when it is not necessary. An overly conservative choice will cause the maintenance costs to rise.
Worst would be a choice that was a low priority when it should have been a critical one. The result of too low a priority would be insufficient maintenance and operator care and an increased risk of a disastrous failure. My experience is that when the criticality rating is then used to determine what maintenance strategies to apply the natural inclination to minimise the cost of doing maintenance means about 20% of important equipment get insufficient and inadequate maintenance and care.
The second drawback of standard risk-based equipment criticality rating methods is that they assume that doing appropriate maintenance is sufficient to control risk to the operation. Little is done to identify what operating practices need to be applied and what level of skills, knowledge and intelligence is required for person operating and maintaining the plant and equipment. The assumption that maintenance alone is sufficient to manage production-loss risk is extremely far from the truth! Risk management is a multi-function and cross-departmental requirement.
The problems of subjective choices and justifying proper and thorough maintenance and operating practices are solved by using true failure costing. True failure-based costing applies Activity Based Costing to identify every cost to the organisation of each failure mode. The total cost of the most significant failure becomes the equipment priority rating.
True Cost of Failure Based Criticality Rating
Activity Based Costing (ABC) is an accounting technique that identifies the total and complete costs of the activities used to perform a function or produce a product. ABC applied to equipment criticality allows an organisation to determine the actual cost throughout its organisational structure associated with overcoming a failure.
A failure absorbs resources that had otherwise been assigned to produce the organisation’s products and deliver services. Once there is a failure the organisation’s money, effort and resources are then used for no useful profit, only to minimise loss; a loss that should not have happened in the first place! True failure-based costing is a powerful tool for measuring business failure costs since it itemises each expense in every department affected and identifies its make- up. It provides a means of pinpointing business process inputs into the incident and the subsequent costs and losses incurred by the operation because it.
All business decisions need to have a firm financial basis in fact. Subjective business decisions often cannot be substantiated and if wrong they may cause unnecessary cost impacts on the organisation. Wrong equipment criticality decisions can have catastrophic financial results. The practice of decision making based on the best opinion of people who may have insufficient knowledge and experience can be overcome with the true failure cost method.
Since true failure costing identifies every cost that can result from a loss incident it is practical to now base equipment criticality on the actual financial effects of equipment failure to the business. The more expensive the loss of equipment is to the business then the higher its criticality. The real dollar cost of the incident becomes the equipment criticality rating for the item of plant.
By taking one item of equipment at a time and identifying the true cost of failure for it, a believable cost-based rating scale can be developed. The financial cost of the failure is the scale rating. The greater the cost of the equipment failure to the organisation then the higher is the equipment criticality rating.
A Sample True Cost Based Equipment Criticality Scale
Using the previous family car example and applying the true failure cost approach, a more robust, financially-sound criticality rating results. This rating is based on the actual costs if a failure incident were to occur.
To start the analysis, process an assumption is made that the equipment has totally failed in isolation. The very worst outcomes and their consequences are envisioned and costed. This includes death of employees, destruction of the environment and major plant and equipment loss in those situations where such consequences are plausible. Once the worst outcome cost is known, the other possible and less serious failure scenarios for the equipment are then modelled.
The true failure cost method is applied progressively when determining equipment criticality. It starts with assuming the complete item of equipment has failed. The consequences of all the possible failure modes that could cause such a failure are costed. Failure mode by failure mode, the effects and consequences of each equipment failure on the whole organisation, its departments and customers are priced. The final costs are the equipment criticality ratings.
If desired the analysis can then move down to each assembly in the equipment. Again, each possible failure mode of each assembly with their financial and production delay consequences for the organisation can be costed in full detail. The cost becomes the criticality rating for the assembly. The process can continue to even component part failures if required.
The ABC equipment criticality rating method captures every cost caused by a failure incident. The amount of computation required to calculate equipment criticalities by this method is best done on a computer drawing from a well-developed data base of organisation-wide costs. The data needed would include costs for materials, services, outside resources and internal labour. The internal labour costs include production, maintenance, administrative and management personnel costs. Once the data base is established it becomes an extremely quick and powerful method to model the real cost of failure for any item of equipment.
A full range of possible scenarios is costed to provide complete understanding of all the risks and their consequent costs across the whole operation. Understanding the full risk profile business- wide allows better design, operating and maintenance decisions to be made to manage those risks.
As well as the financial costs of a failure it is necessary to identify the length of time it will take to recover from the incident. Often the time lost in returning equipment to operation is a far more critical factor than the cost of the repair since the business cannot function for that entire period. It has no means to generate revenue from its plant and machinery, yet its fixed costs are still accumulating.
The selection of the best means to prevent a failure can only be made when the implications of the failure across the whole organisation are fully understood and appreciated. With a full knowledge of the failure consequences and costs on the total business the extent of required prevention measures becomes obvious. It is then possible to easily justify necessary and sufficient systems, methods, training, and procedures to prevent failures and maximise production.
Table 2 shows a possible True Failure Cost Criticality Rating for the family car example previously used.
The dollar costs are the equipment criticality rating. In Table 2 we can see that at a replacement cost of $20,000, damage to the car body carries substantial risk to its owner. Damage to the chassis at $15,000 to repair comes next. Wrecked suspension cost of $8,000 is third. The engine at $6000 is not the most expense of failures, but there is a substantial time delay in getting the car back on the road. The standard equipment criticality rating systems normally used would not produce such a thorough understand of the failure consequences to the organisation (the family).
Notice that the True Failure Costing method for equipment criticality reflected in Table 2 makes it clear where responsibility lays for protecting the equipment from harm. It is clear who the responsible people are for each mitigation action. Whether the risk’s management requires proper operation, or it requires maintenance, or it requires monitoring, is made self-evident for all. The
financial consequences of not doing the right actions to mitigate the risk are also clear to everyone. True Failure Costed equipment criticality allows the responsibly for the well-being of the plant and its operation to be easily and unambiguously specified.
What is often discovered with the True Failure Cost method is that the failures which were not considered important by the standard risk-based equipment criticality rating methods are awfully expensive. These losses received little attention using standard criticality rating methods because, so few failures have occurred that people dismissed them as unimportant because of their low “one-in-a-million” chance of occurring. What the True Failure Cost approach tells us is that, though the equipment may not fail often, when it does fail, it will be expensive to fix and have massive consequences for production and profit loss. It only needs a few large catastrophes close together in time to destroy an organisation’s profitability.
The True Failure Cost method highlights that many risks to the business previously considered minor are high and they require a management plan be put into place to address those risks. The frequency of occurrence maybe low but the cost consequences are massive and so the real risk for the organisation is high (risk = frequency x consequence).
In the case of a family car the risk management plan involves having a skilled operator (the driver) who knows how to drive well and does not put the car into situations where it can be damaged. The short-term risk management practices also involve the driver noticing when things are not working as they should and reporting them in time to be rectified before a full failure develops.
Both the short term and the long-term risk management, operating and maintenance practices are clearly identifiable and justifiable once the full and real cost of a failure and its consequences are seen in real money terms.
This method of rating your plant and equipment criticality provides a complete picture of what really happens to your business when you have equipment problems in the operation.
Mike Sondalini
www.plant-wellness-way.com
Leave a Reply